Table of Contents
The method statement for plumbing installation and maintenance should include the following important aspects:
Scope
The work procedure for general plumbing installation and related maintenance and repair work is highlighted in this Method Statement (MS).
Health and Safety Risks
Before starting any work, the team shall rigorously abide by the Manufacturer’s/ Client’s/Consultant’s Health & Safety requirements for handling and using the materials and ensure that all involved individuals shall be informed of the same.
Below are the general safety guidelines:
Make sure the work area is clean and safe.
Every employee must use safe working procedures.
Wearing a safety helmet, safety shoes, coveralls, gloves, goggles, and a face mask if needed are all required pieces of safety equipment.
Extra care must be used when using tools at a high level to prevent falling. The proper safety harness must be used and attached while working when working at a high height.
Make sure there is enough lighting available for all installation and testing phases.
Any accident should be reported to the on-duty HSE Engineer or Officer.
For the installation of any electrical equipment, panels, cables, wires, and accessories, make sure to secure any required electrical isolation permits.
Responsibilities
Project manager
The project manager is responsible for the overall project execution.
In addition to attending review meetings, he is responsible for resource management and progress monitoring.
Overall, he will be responsible for completing the project on time and in accordance with all contractual obligations.
This might interest you: Method Statement for Gully Trap Installation
Method to be Performed
- Procedure
- Site Inspection
- Pre-installation Meeting
- Technical Submittals
- Project Schedule/Program Submission
- Procurement
- Delivery of Materials to Site
- Installation (using the below method)
- Testing (examining the functionality and all connections)
- Commissioning
- Handover
Required Equipment
PPE-safety gloves, boots, high-visibility jacket, and helmet. When using cutting or grinding tools, wear safety goggles.
Scaffolding
Ladder
Power Drill
Standard toolbox
Drilling Machine
Safety and Health Requirements
During this work, all safe practices will be used.
Use of the required respiratory and personal protective equipment is required.
For the works, enough access for the labor force and equipment must be provided.
Checked for maintenance documents are all machinery.
All debris, steel waste, nails, and other materials must be removed from the site.
Before beginning any work, toolbox talk will be conducted.
The necessity for close supervision of safety requirements shall be provided.
Barriers, lighting, and other necessities must be provided and kept in good condition.
Preparation
Report to the Project Office or Work Site, notify the Project Engineer or Manager of your arrival, and, if needed, receive a Permit to Work (PTW).
As needed by the facility manager or principal contractor, attend any orientations or inductions.
Wear personal protective equipment at all times.
Move/take the required tools, machinery, and equipment to the site work area.
Always cordon off the work area if it is needed to preserve health and safety.
Make that the area to be worked on, the departure points, and the safe entrance and egress are all appropriately accessible, clean, and obstruction-free.
Check for damage or defects in any electrical, hand tools, or equipment, and remove faulty or damaged items from service as soon as possible.
Never leave any equipment, vehicles, machinery, or tools unattended.
At the end of each shift, make sure the work area is left safe.
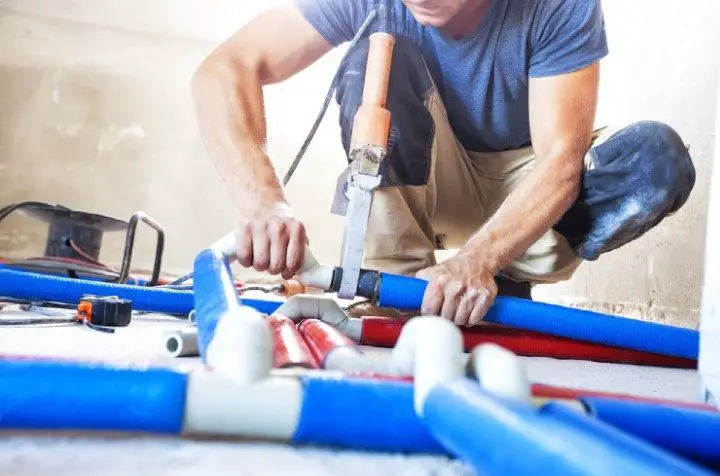
Maintenance and Repair Work
To isolate water supplies, consult with other contractors, outside vendors, and the Facilities Manager (FM).
Where required, isolate the hot and cold water pipes.
Where it is required, drain the water system.
Use the cable/pipe detector to first check the actual location of any installation in walls and underground for any electric lines or pipes before chasing out the walls.
Mark the wall appropriately for the area that will be checked.
When installing on plasterboard walls, carefully use a cutter to cut out the installation.
Utilizing a hand bolster, chase out the plaster walls.
Remove any skirting boards that are mandatory by inserting the bolster chisel behind the board and slowly pulling it away from the wall.
To ensure the area below the board is clear, any floorboards that are required to be lifted up should first be checked with the cable/pipe detector.
On some floors, it may be mandatory to reset the circular saw to a depth of 20-22 mm and make a second cut down the length of the board through the Tennon on both sides.
Remove all nails by using the bolster chisel to lift the board.
Avoid leaving open floorboards and upturned carpets for longer than necessary. Where there is a chance that other contractors will approach the project site, vital warning signs must be erected. Attention will be paid to the trip hazard created by removing the carpet and lifting floors.
Replace the damaged pieces.
Ensure that plastic pipework and waste pipes are linked properly.
Employees/staff will adhere to all safe usage recommendations where plastic pipe is linked to solvents.
Prepare the pipes for solder junctions where solder work needs to be done.
Ask the Facilities Manager (FM) for the proper hot work permit.
During hot work, make sure the appropriate type of fire extinguisher (FE) is available.
Heat shields should always be used to protect the surrounding area.
Ensure appropriate ventilation when working with solder.
All mandatory joints must be soldered.
Examine each joint.
To reactivate water supply, speak with the Facilities Manager (FM).
Verify the finish’s quality and watertightness once again.
Check for successful completion and chlorinate the system if needed.
Ask the Facilities Manager (FM) to look over the work.
The Facilities Manager (FM) a completion certificate and chlorination.
Make appropriate housekeeping while packing tools and equipment.
Where hot work has been conducted, maintain a fire watch for 2-4 hours.
After the task is finished, go to the site office and sign a permit to work.
tag: # Method Statement for Plumbing Installation and Maintenance