Table of Contents
What is the Method Statement for Fire Alarm System Installation?
A Method Statement for Fire Alarm System Installation is a document that outlines the step-by-step procedures and guidelines for installing a fire alarm system in a building or facility. It provides a detailed description of the activities, equipment, and safety measures to be followed during the installation process.
Scope
This procedure defines the project’s fire alarm system installation and supply method.
This document provides installation information for fire alarm systems.
Work preparation.
Delivery and inspection of the material after it has arrived on site.
System Installation
Definitions
Project Quality Plan (PQP)
PSP Project Safety Plan
QCP Quality Assurance Procedure
HSE Health, Safety, and the Environment
MS Method Statement
QA/QC Quality Assurance and Quality Control
WIR Work Inspection Request
MIR Material Inspection Request
FAS Fire Alarm System
Health, Safety & Environment HSE
Strictly follow the manufacturer’s Health and Safety Guidelines for Material Handling and Use.
Make sure that everyone who is involved will be aware of it.
All safety precautions are included separately in the project safety plan, and specific safety measures must be followed where applicable.
Operation
Material
The Engineer will approve the materials utilized.
Sizes and routing will follow the authorized Shop Drawings.
Protection and Storage
Deliver all components and pieces to the job site, fully labeled in accordance with shop and approved CAD drawings created for this work.
Keep above ground, fully shielded from the elements and building activity, and store in accordance with the manufacturer’s recommendations.
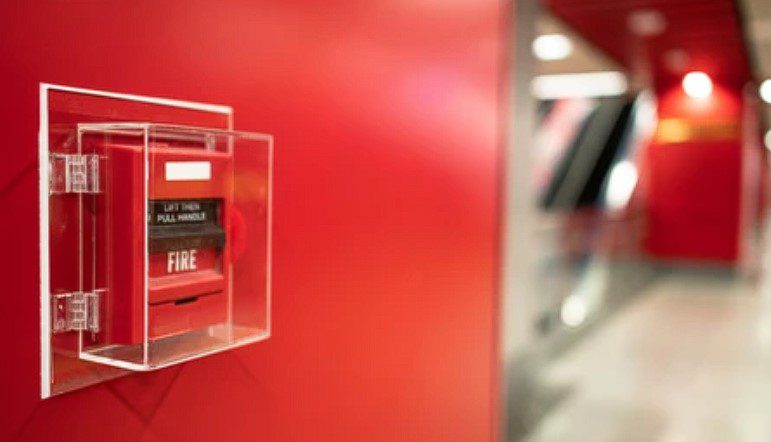
Installation
Pre-Installation:
Ensure that civil clearance has been completed before beginning the installation.
The installation will be carried out in accordance with approved shop drawings and project specifications, as well as manufacturer suggestions.
Installation:
Before making connections, make sure that the hardware and devices are NRTL listed for usage with fire alarm systems.
Make addressable connections to the following systems and devices using a supervised interface device.
Install the interface gadget a maximum of one meter (three feet) away from the device controller.
When such feedback is available at the device or system being controlled, establish the following addressed confirmation connection:
- At the firefighter smoke-control system panel, an alarm is initiated and connected to the smoke-control system (smoke management).
- Link to the pressurization systems for the staircase and elevator shaft that initiates an alarm.
- Smoke dampers in specific duct systems for air conditioning.
- Connection to the elevator recallss system and its components that initiate an alarm.
- The link initiates an alarm to turn on the emergency lights control.
- The alarm-starting connection turns on fuel and gas emergency shutoffs.
- Valve supervisory switches with supervisory connections.
- Supervisory connections at each dry-pipe sprinkler system’s low-air-pressure switch.
- Supervisory connections at the trip breaker for the elevator.
- Supervisory connections in the event of a dead-phase or phase reversal condition during a fire pump power outage.
- supervisory connections at the control panel for the fire pump engine.
Assembling together the components:
The devices/peripherals (control and monitoring modules, break glass, duct detectors, beam detectors, smoke detectors, heat detectors, and break detectors) are connected to the control panels in a Class A circuit.
The Control panels and the Speakers & Panel with Strobes are connected on a Class A circuit.
Additional 2c x 2.5mm2 FP200 cable is required for smoke detectors with sounder bases for the activation of the sounders units. 2 Core 1.5mm2 FP 200 cable will be used for connecting the Initiating Device Circuits (IDC) to the panel.
Additional 2c x 2.5mm2 FP200 cable is required from the FACP for the speaker with strobe for the activation of the strobe unit allied on vertical walls the run of conduit will be kept straight.
Two core 1.5mm2 FP 200 cables will be used for the cabling of the Speakers with the Panel.
For the installation of fire alarm equipment, adhere to NFPA 72.
Heat detector or a smoke detector
NFPA 72, “Smoke-Sensing Fire Detectors” and “Heat-Sensing Fire Detectors,” must be followed.
The maximum smooth ceiling spacing is 30 feet (9 meters).
Surface-mounted fire alarm control unit with cabinet tops no higher than 72 inches (1830 mm) from the finished floor.
Install the announcer such that the top of the panel is no higher than 72 inches (1830 mm) above the finished floor.
Screen for Fire Alarm Control
Install the provided semi-recessed backbox in accordance with the authorized shop drawings.
An unswitched SPUR outlet above the FACP that is concealed above a false ceiling must give power to the FACP. The SPUR switch that cannot be switched must be its own branch circuit.
Before placing all of the field cables inside the rear box, it must be clean and clear of dust.
Automatic Call Point
Install the 2″ x 4″ back box recommended for recessed installation in the locations indicated on the approved shop drawings.
In accordance with the manufacturer’s instructions, install and terminate the Manual call point.
Control and Monitor Modules
Near each sprinkler valve station and/or water flow detector that is required to be supervised are water-flow detectors and valve supervisory switches. The module must be mounted inside a 2″ x 4″ back box that is recommended, and it must be wired to the sprinkler valve station and/or water flow detector using GI flexible conduit.
AHUs, FAHUs, elevators, doors with access controls, public address systems, etc. The Control module must be put inside the advised 4″ x 4″ back box and wired to the equipment to be interfaced, which is required to be controlled in a fire event.
According to the manufacturer’s instructions, install and terminate the Monitor and Control modules.
Smoke and Heat Detectors
Smoke and heat detectors mounted on ceilings:
At least 100mm from a sidewall to the near edge. Detectors should be mounted on the underside of joists in exposed solid-joint construction. Install smoke and heat detectors on smooth ceilings at a distance of no more than 7 meters and 9 meters, respectively.
Sounder and Flasher
Install the recessed 4″ x 4″ back box at the appropriate locations in accordance with the approved shop drawings.
As per the manufacturer’s instruction, install and terminate the Sounders.
Finding Errors In The Emergency Battery System
Faults in Battery Chargers:
Battery Charger Faults that may develop during the course of a panel’s operating life. You might notice one of the following faults: a charger that is 2% out of range, a battery charger with an improper supply, etc. To properly measure the output voltage, follow the steps listed below:
- Disconnect the batteries, turn off the system, and cut the power and harnesses from the Power Supply to prevent damage to the system.
- With the batteries removed, attach the multimeter to the battery leads, turn on the power, and take a voltage reading.
- Find the difference between the actual voltage and 27.6 volts.
- Earth ground faults that are positive or negative
The detection of either positive or negative Earth Ground Faults is possible with Fire Panels.
In electrical circuit that is shorted to ground develops an Earth Ground Fault.
Wire installation:
Unless they are inside consoles, back boxes, workstations, or countertops, install cables in cable trays and raceways. Keep cables and raceways hidden everywhere but in unfinished areas.
The maximum length of the cable when using CAT-6A type cable is 90 meters. of the manufacturer’s advice, which the supplier of structural cabling systems will give.
Follow the requirements for raceways and boxes in Division 26 Section “Raceways, Boxes, Cable Tray, Cable Ladder, and Trunking.”
Where possible, conceal cables and conductors in accessible ceilings, walls, and floors.
Wiring within Enclosures
In enclosures, bundle, lattice, and train cables.
Connect to termination points without extra space between them and without going above the manufacturer’s bending radius restrictions.
Grounding
Meet the requirements for grounding conductors and connectors in Division 26 Section “Grounding and Bonding for Electrical Systems.”
Observe the sections of the ADDC Electrical Wiring Regulations.
Metallic equipment should be grounded to the system grounding bus bar using a conductor that is no smaller than that stipulated in the ADDC Electricity Wiring Regulations, Sections.
Identification:
Determine which system components, wiring, and cabling adhere to ADDC Electricity Wiring Regulations. Observe the identification requirements outlined in the project specifications.
Programming
Before final testing and commissioning in accordance with Consultant requirement and scenario of the system, programming of the system must take place after making sure all the system requirements were correctly installed by Subcontractor and Supplier.
The testing and commissioning of the system were filed separately for this system, and they covered every step of the testing and commissioning process.
Technical Support
After the installation is complete, the system trade installation supervising technician is responsible for instructing the Consultant Engineer, Construction Site Manager, and others on the programming and proper operation of the system.
The staff will choose the most convenient time to schedule this instruction.
All of these instructions must be adequately documented.
Making ensuring that the installation of the system equipment complies with authorized shop drawings, approved specifications, and manufacturer recommendations, WIR will be issued for Consultant approval.
Responsibilities
Project Engineer
Ensures that the work is carried out in accordance with the shop drawings, authorized method statement, and contract specifications.
Shares duties among his construction and offer all essential information.
Reports to the Project Manager and monitor the work’s development with respect to the work program.
Coordinates with the safety officer and ensures that the tasks are carried out using a safe working method.
Foreman
The foreman will carry out his tasks by maintaining daily coordination with the site engineer to ensure the correct distribution of the workforce in the required and planned locations.
To ensure that his charge hand and assistant foreman are aware of the task requirements and have sufficient information to carry out their jobs effectively.
To ensure that the daily work is progressing as planned and to inform the site engineer of any requirement for additional resources.
To ensure, in cooperation with the site engineer, that the manpower involved in the tasks is moving as agreed upon and planned for the tasks.
Maintain control over the disposal of waste materials in accordance with the site engineer’s recommendations.
To maintain safe work and proper site upkeep, to follow the proven safety procedures, and to further ensure that other members of his working team are aware of the same in order to prevent accidents and losses. To follow full coordination with the safety officer.
Communicates to the site engineer the locations that are ready for inspection.
The distribution and control of materials are within the purview of the foreman and the storekeeper.
Safety Engineer
Ensure that everyone is aware of the HSE plan and that all safety measures are being implemented in accordance with it.
Verify that all the safety measures in place are sufficient to guarantee secure working conditions on the site.
Verify all work being done on the site, and provide training for those who will be responsible for accident prevention.
Maintain the site’s cleanliness and order.
Technician
Constant coordination with the subcontractor Site Engineer for the purpose of carrying out work and distributing all resources effectively.
Daily reports on the work are produced and coordinated with the site engineer for future planning.
Complying the subcontractor’s basic design guidelines, especially those relating to engineering and safety.
Any form of unexpected event or requirement should be discussed in person and reported right away to the site engineer.
Storekeeper
Being in charge of all store operations includes making sure that the materials delivered to the site are stored in a way that keeps them safe from rust and damage.
In coordination with QA/QC and the appropriate Engineer, one shall acknowledge the receipt of materials at the site.
Manpower
Technicians
Experienced Chargehand
Materials
FAS Accessories and Components.
Tools & Equipment
The following equipment will be utilized for installing fire alarm systems:
- Power supply
- Drilling apparatus
- Toolbox
- Tape Measures
- Calibrated Multimeter or Ohmmeter
- Scaffolds / Ladders
- Hammer
To ensure the best possible ability to safe work, safety requirements products like safety shoes, safety helmets, safety glasses, fluorescent vests, and safety gloves are required.
Waste Management
The authorized dumping ground will receive the trash generated by the work.
Special Control Measures
The scope of work will require the general controls against safety, the environment, and quality listed below; we are not subject to particular controls.
PPE must be worn properly at all times.
Where applicable, a permit to work at heights greater than 2 meters.
Where applicable, a lifting operation permit (using a crane).
If applicable, a confined space permit.
The risk assessment and approved work method statement will be made available on-site.
This Method Statement for Fire Alarm System Installation and risk assessment must be explained to all employees performing the work.
QA/QC Documentation
The following documentation should be reviewed in connection with this method statement:
Work Inspection Request WIR for the installation of fire alarm system
Report on the tests for continuity and insulation resistance.
Distribution
For information, action, or comments, a copy of this method statement must be issued to the following:
Project Engineer
Foremen
Safety Engineer
Technician
tag: # Method Statement for Fire Alarm System Installation