Table of Contents
- What is the Method Statement for Interior Fit-Out?
- Overview of Interior Fit-Out
- Importance of Method Statements in Interior Fit-Out Projects
- Purpose of Method Statement
- Project Overview
- Work Methodology (Procedure for Task Execution):
- General Information
- Access/Egress and Safety Procedures
- Delivery and Security
- Permits
- Fall Protection & Rescue Measures
- Emergency Plan
- First Aid
- Emergency Services
- Building Entrances
What is the Method Statement for Interior Fit-Out?
The method statement for interior fit-out is procedural guidance which acts as a critical document that aligns the fit out project with safety, efficiency, and regulatory compliance, thereby laying the foundation for a successful and sustainable outcome.
Overview of Interior Fit-Out
Interior fit-out refers to the process of enhancing and customizing the interior spaces of a building to meet specific functional and aesthetic requirements. This intricate phase of construction involves the installation of elements such as partitions, ceilings, flooring, and fixtures, transforming a bare structure into a functional and visually appealing environment.
Importance of Method Statements in Interior Fit-Out Projects
Method statements play a pivotal role in the successful execution of interior fit-out projects. These documents outline the systematic approach and procedures that will be employed throughout the project lifecycle. As complex and multifaceted endeavors, interior fit-outs require careful planning and execution, making method statements essential for ensuring a structured and organized workflow.
Purpose of Method Statement
Definition and Purpose
A method statement is a comprehensive document that details the step-by-step procedures and methodologies to be employed in the execution of a specific task or project. In the context of interior fit-out, the method statement serves as a blueprint, providing a clear and systematic guide for all stakeholders involved in the project.
Importance in Ensuring Safety and Efficiency
One of the primary purposes of a method statement for interior fit-out is to prioritize safety. The document outlines safety protocols, risk assessments, and precautionary measures to safeguard the well-being of workers and occupants. By incorporating safety considerations into the method statement, the project team can mitigate potential hazards and create a secure working environment.
Additionally, method statements contribute to efficiency by establishing a structured workflow. Each task is outlined in a logical sequence, ensuring that the project progresses seamlessly. This systematic approach enhances productivity, minimizes delays, and optimizes resource utilization.
Compliance with Regulations and Standards
In the dynamic construction industry, adherence to regulations and standards is paramount. Method statements serve as a tool for ensuring compliance with local building codes, industry standards, and safety regulations. By incorporating legal and regulatory requirements into the document, the project team demonstrates a commitment to delivering a fit-out that meets or exceeds industry standards, reducing the risk of legal complications and ensuring the longevity of the constructed space.
Project Overview
Task Description and Location:
This documentation outlines the comprehensive on-site activities to be undertaken by fit-out contractor and subcontractors.
The scope of work includes, but is not limited to, the following:
Construction activities involving Cat B fit-out works of existing office space. This encompasses:
Installation of new fire-rated and non-fire-rated stud partitions
Implementation of glazed partitions
Installation of associated doors and joinery
Tape and joint procedures and wall decoration
Installation of new floor coverings in the canteen and lobby
Establishment of a new tea station
Mechanical and electrical works encompassing:
- Cat B MEP installations tailored to the new layout configuration
- Implementation of general lighting and task lighting
- Installation of fire alarm systems
- Deployment of access control systems
- Implementation of intruder alarm systems
- Installation of CCTV systems
- IT data installation
- Deployment of emergency lighting
- Installation of new HVAC systems
- Provision of plumbing supplies and waste management for the tea station
- Establishment of the communications room, including 4nr racks and UPS
- Commissioning and testing of all installations
Each subcontractor is obligated to submit their own Risk Assessment and Method Statement (RAMS) document for review by Fit-out Contractor before the commencement of any works. Only upon approval will the works be permitted to commence.
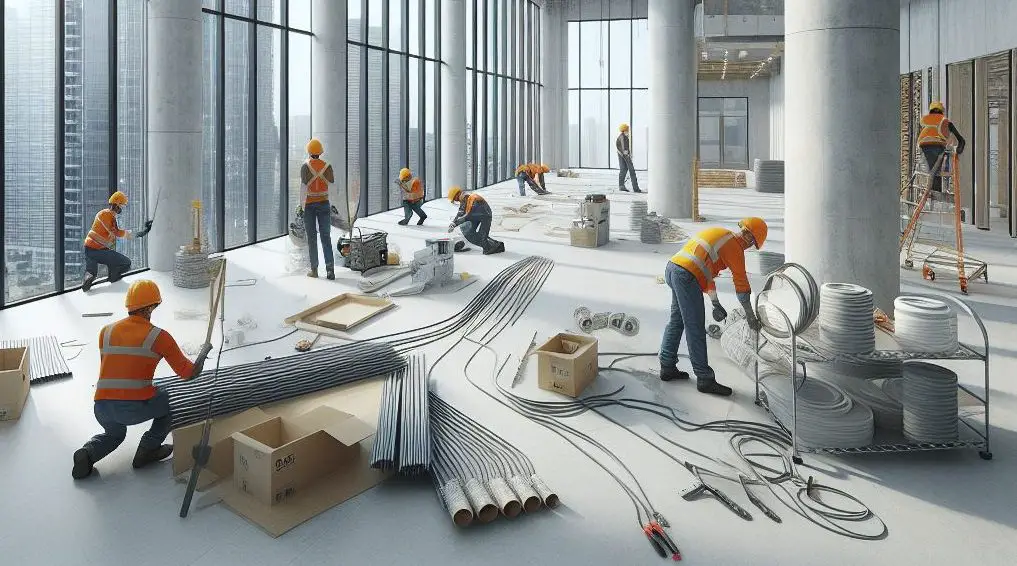
Work Methodology (Procedure for Task Execution):
Site Setup and Additional Details
- Upon arrival at the site, communication will be established with the Fitout Site Manager, and mutually agreed-upon access routes will be determined.
- Parking arrangements are available on-site, and specific details should be verified with the Fitout site manager.
- An induction program must be completed for each Contractor/Operative attending the site. Upon completion, relevant details will be recorded in a register, utilized by site management.
- Operatives are required to review the scope of work, the method to be undertaken, and associated risks.
- A comprehensive Method Statement will be issued for each element of work conducted by Fitout contractor.
- The Fitout Site Manager will explain control measures for each work element, and RAMS will be signed off as read and understood.
- The site manager will ensure the implementation of all Covid-19 control measures (as per risk assessment) before subcontractors’ arrival.
- Operatives will establish a safe work zone around the designated areas. Once the area is segregated, work equipment will be brought in.
- Material, equipment, and site setup will be transported to the site, distributed to the compound loading area, and stored as per site management agreement.
- RAMS will be reviewed and communicated with relevant operatives.
- Works will be supervised as required, with specific adherence to the RAMS.
- The electrical contractor will assess the area and perform isolations of any electrical services.
- The Fitout site manager will collaborate closely with center management, ensuring staff safety throughout the process.
- A “Clean as You Go” policy will be enforced consistently. The location for waste disposal in the skip will be confirmed with the Fitout site manager.
Key Considerations for Subcontractor Management
1. The fitout supervisor overseeing subcontractors must comprehend:
- The subcontractor’s scope of work
- Responsibilities for supply arrangements
- Reimbursement procedures for the subcontractor
2. The subcontractor must:
- Adhere to project safety requirements
- Deliver work of acceptable quality
- Adhere to the project schedule
- Ensure that subcontractors receive timely access and information, avoiding delays caused by the contractor or other subcontractors.
- Subcontractors must acknowledge receipt of issued drawings and information.
- When applicable, subcontractors should provide drawings in line with the project schedule, including allowances for obtaining necessary approvals from the contractor or client.
- Communication with subcontractors should only be conducted by the contractor’s designated responsible staff to prevent confusion and errors resulting from conflicting instructions.
- Subcontractors should have appropriate quality, safety, environmental, and industrial relations procedures in place, compliant with project requirements.
- Commencement of work by subcontractors is contingent upon the existence of a duly signed contract, along with the submission of the requisite Risk Assessment and Method Statement (RAMS) and insurance documentation.
- The contractor has the authority to approve the personnel, equipment, and subcontractors enlisted by the subcontractor.
- Personnel from the subcontractor undergo the project induction program organized by the contractor.
- Timely and efficient handling of correspondence originating from the subcontractor is ensured.
General Information
Housekeeping
- Adherence to all established good practice guidelines for workplace housekeeping.
- Rigorous implementation of a CLEAN AS YOU GO policy on the site under the management of IIS.
- Proper securing of all work equipment, chemicals, and substances when not in use to prevent unauthorized access or accidental contact.
- Placement of warning signage and barriers, if necessary, around the work area before the commencement of works to prevent unauthorized access.
- During the works, maintaining cleanliness and tidiness in the area with clear walkways as appropriate.
Work at Height
- Compliance with all current legislation and codes of practice concerning working at height.
- Selection of suitable access equipment, such as a mobile tower for main areas and ladder access for small rooms, providing a safe working platform. The equipment will be inspected before and during its use, and proper edge protection will be ensured.
Harmful Substances
- Substitution of hazardous substances with non-hazardous alternatives whenever possible.
- Authorization for the use of chemicals/substances limited to individuals fully conversant with their properties.
- Maintenance of adequate ventilation when using hazardous chemicals/substances.
- Proper storage of chemicals/substances in closed containers in a secure location when not in immediate use.
- Collaboration with site management/principal contractor if well-vented workplace provision is impracticable during the works.
Waste Disposal
- Proper containment and disposal of any contaminated or hazardous waste resulting from the conducted works by a specialized waste management company.
Attached below are the Risk Assessments that should be reviewed in conjunction with this document. Additionally, the particulars of all tools and equipment slated for use, as well as the prescribed Personal Protective Equipment (PPE), are outlined below.
Type of Tool/Equipment | Type of PPE | Usage |
---|---|---|
Skip & Material Trolley | High Visibility Vest | Compulsory at all times |
Hand Tools, Leads, and 110v Power Tools | Safety Footwear | Compulsory at all times |
Cordless Drills | Safety Helmet | Compulsory at all times |
Decoration Materials | Safety Gloves | When using hand tools, power tools, etc. |
Barriers, Cones, Hazard Tape, and Signage | Safety Glasses | Compulsory when cutting |
Ear Protection | Compulsory when cutting, etc. | |
Dust Mask | Compulsory according to Risk Assessment |
Please ensure that the accompanying Risk Assessments are thoroughly reviewed and the specified tools and equipment are utilized in accordance with the outlined PPE requirements for each activity.
Communication of Method Statement and Changes:
1. Communication of Method Statement to Workforce
- Before the initiation of any work, the Fitout Supervisor specified in this Method Statement will conduct a briefing for the operative(s) tasked with the work, covering this Method Statement and associated documents.
- Operatives are required to sign the Method Statement, confirming their reading and understanding of it and expressing agreement to work in accordance with it and the associated documents.
2. Communication of Changes to Method Statement
- In the event of any necessary alterations to the details in this Method Statement or its supporting documents during the course of the work, all operatives involved will undergo a re-briefing. They will be requested to re-sign the updated Method Statement.
3. Monitoring, Inspection, and Safety Measures:
Area Monitoring and Inspection During Works
- Operatives are responsible for ensuring the safety of their working areas. Any doubts or concerns should be promptly reported to the site supervisor.
- The supervisor will conduct daily safety monitoring and address or report any identified issues.
- Health & Safety Consultant will perform periodic safety, health, and environmental audits.
Protection of Other Trades and the Public
- Coordination with other trades through daily on-site communication and the use of barriers to establish exclusion zones.
- Public safety ensured through the display of clear signs visible to pedestrians, indicating ongoing construction along the site perimeter and entrances.
- Entry to the site involves mandatory sign-in/out through the QR code system managed by the site manager.
Environmental Controls
- Strict adherence to security rules.
- Waste disposal follows a drop-load-go system, with regular checks on equipment likely to cause environmental incidents.
- Waste Management plan submitted for review, focusing on reuse, salvage, and recycling of materials.
Access/Egress and Safety Procedures
Access/Egress
- Site access from car park areas via stairs or lift to the top floor.
- The project supervisor or the Project Supervisor for the Construction Stage (PSCS) ensures safe access and egress to work areas.
- Contractors must not obstruct or jeopardize normal access outside the immediate work area.
- Adherence to local safety instructions, including speed restrictions.
Delivery and Security
- Fitout contractor is responsible for all delivery arrangements for their own and subcontractors’ equipment and materials.
- Security does not accept deliveries on behalf of contractors.
Permits
- Fitout operatives require permits from management before commencement.
Fall Protection & Rescue Measures
- Adherence to the hierarchy of control for work at heights.
- Planning and supervision of all work at height, with a prohibition on throwing or dropping materials from heights.
- Encouragement of podium steps or equivalent where feasible.
Additional Information/Remarks:
- All exposed openings or edges will undergo protection measures to mitigate risks for individuals entering the project site.
- A dedicated welfare facility adjacent to the work site, organized by FC Fitout, will be provided. Contractors are mandated to utilize the allocated toilet and washroom facilities, ensuring they are left in a clean and organized state.
Emergency Plan
The Emergency Plan is activated under the following circumstances
- Uncontrollable fire within the site despite initial efforts with provided fire extinguishers.
- On-site explosion.
- Situations involving persons trapped with an immediate risk to health and safety.
- Structural collapse leading to trapped individuals or potential danger to persons on or affected by the site.
Actions for Persons Discovering a Fire/Emergency
If a fire is discovered, personnel must:
- Alert others.
- Attempt to extinguish a small fire (size of a wastepaper bin) using a fire extinguisher. For larger fires, evacuate immediately.
- Inform the Site Supervisor.
- Proceed to the Assembly Point.
Actions for Site Supervisor:
The Site Supervisor, upon being alerted of an incident, will:
- Alert site personnel and direct them to the Assembly Point.
- Obtain outline details of the emergency and notify emergency services.
- Contact the First Aider in case of injuries and provide directions to the location.
- Guide emergency services onto the site.
- Inform the Site Supervisor.
- Go to the Assembly Point to assess the situation.
- Check with contractors for any missing operatives using the daily sign-in sheet as a checklist.
- Receive and brief emergency services, providing details of emergency water supplies/hydrants if necessary.
Actions for All Contractors:
All contractors are required to:
- Isolate plant/equipment only if it is safe to do so.
- Proceed directly to the Assembly Point and report to the Site Supervisor.
- The Senior Person from each contractor must check for missing individuals.
First Aid
- A first aid kit must be brought to the Assembly Point, and trained First Aiders are to report there.
Emergency Services
- At the Assembly Point, Site Management will receive and brief emergency services, providing details of any missing personnel.
Building Entrances
- Entrances to the building must remain unobstructed at all times as they serve as access points for firefighters.
tag: # Method Statement for Interior Fit Out