What is a Nonconformance Report?
A nonconformance report, often known as an NCR, is a construction-related document that deals with work that doesn’t adhere to quality standards or specifications.
The report, which describes the issue, how it happened, and how to keep it from happening again, is utilized for the quality control process. The NCR can also be used to reach an agreement with the customer and record any subsequent corrective modifications.
Table of Contents
- What is a Nonconformance Report?
- What are the Contents of the NCR?
- 7 Steps for Managing Nonconformances in Construction Quality
- Non-Conformance and How to Minimize It
- What Are the Various Types of Nonconformances?
- How are Non-Conformances Found?
- How Are Non-Compliances Handled?
- How Can Non-Conformances Be Prevented or Reduced?
- Analysis of the Root Causes
- Long-Term Remedial Action
- Validating the Approach’s Effectiveness
- The Value of Digital Tools Such as Non-Conformance Management Software
- Conclusion-Nonconformance Reports NCRs in Construction Industry
What are the Contents of the NCR?
The following is an example nonconformance report’s contents:
- Significant parties in the NCR and the standards impacted by the NCR
- A description of the corrective action implemented or required
- What steps may be taken to ensure that the issue doesn’t arise again
- Why the work did not conform to the requirements
- What went wrong and the main cause of the NCR
7 Steps for Managing Nonconformances in Construction Quality
Your construction quality control plan should define a systematic approach for managing nonconformances, whether they are tough or easy. You’ll be able to regularly generate high-quality results this way. Furthermore, your clients will have faith that you will strictly limit specification deviations until adequate resolutions are found.
We don’t use the term nonconformance for all problems in quality assurance circles. Instead, we reserve the word for faults that you cannot rapidly or affordably rectify in order to achieve the quality standards of your project.
Here’s an example of a straightforward nonconformance. If you poured a concrete foundation that was one inch too broad, you’d have to chip off the excess inch or modify the foundation to make it fit properly.
This circumstance may not have a negative impact on shape, fit, or function. So redoing it is unlikely to make sense. If you decide to utilize it as-is, you must first obtain clearance from your consumer. Because of this extra step, you won’t be able to deal and close with the fault as quickly, thus you’ll have to treat it as a non-conformance.
Step 1: Make a mark
The first step is to clearly designate the area to prevent misuse or unintended cover-up. This is especially crucial because deciding on the best corrective action or obtaining approval from your consumers can take time.
You’d probably use barrier tape to mark the foundation’s nonconformance. Other nonconformities can be marked with paint, tape, a sticker, or another plainly visible indicator. Make certain that your nonconformances cannot be covered up by accident, no matter how you choose to designate them.
Also, inform your superintendents and inspectors that nonconformances must be marked. More information on conveying your quality policies and procedures may be found here.
Step 2: Maintaining Control
If continuing to work can harm quality or hide the issue, then stop working in the affected area until the nonconformance can be corrected. Your field staff should decide what if any, restrictions they should impose on their ability to continue working in the area.
Inspecting previously completed work of a comparable sort to ensure it does not have identical flaws is also a quality best practice.
Step 3: Documentation
The next step is to complete a nonconformance report after you’ve marked and regulated the nonconformance area. Use the report to detail the deviation and then submit it to a higher authority for disposition (a decision on how to continue).
A non-conformance report also serves as a record of actions done, such as decisions on nonconformance disposition, corrective action, and preventive action.
Step 4: Selecting a Position
Following that, you will decide how to handle the nonconformance.
A nonconformance can be issued in one of four defined ways: replace, repair, rework, or use-as-is. When deciding on the best course of action, keep the descriptions below in mind.
Replace the nonconforming product or material with a conforming product or material to address the deficiency.
REPAIR: Use this corrective action when re-machining, reassembly, reprocessing, reinstallation, or completion of the relevant activities will correct the problem.
REWORK: application of this remedial action when reworking will make the nonconformance acceptable for its intended application, even if not all specification requirements are met. Rework nonconformances must be approved by your customer.
USE AS-IS: Use this remedial action if the nonconforming item is suitable for its intended purpose. Your customer must accept any use-as-is items that do not satisfy all specification requirements.
Remember that if your efforts will not bring the nonconformance back to specification, you must always seek your client’s consent.
Step 5: Corrective Actions
After completing the corrective action, you must ensure that the problem has been eliminated or rectified to the level indicated by the disposition on the nonconformance report.
Corrective action training is sometimes required. This is true if personnel are unfamiliar with the type of repair or rework that must be performed, or if they are unfamiliar with how to install a replacement.
Step 6: Reinspecting
After you’ve addressed the nonconformity, go over your work again and delete your markings.
Step 7: Prevention
Repairing faults discovered during quality inspections is insufficient. You should continuously search for ways to improve quality and avoid similar issues in the future.
As part of your systematic approach, consider the frequency, severity, and detectability of nonconformances observed on current and previous projects. This can be accomplished by examining the company’s quality performance and client feedback.
Training is an important part of prevention that should not be overlooked. Once the root reasons for your nonconformances have been identified, incorporate frequent training and/or toolbox talks aimed at preventing future recurrence.
Defects and nonconformities are common in construction. The difference between a top-tier construction business and an ordinary one is having a methodical strategy for detecting, resolving, and preventing future occurrences.
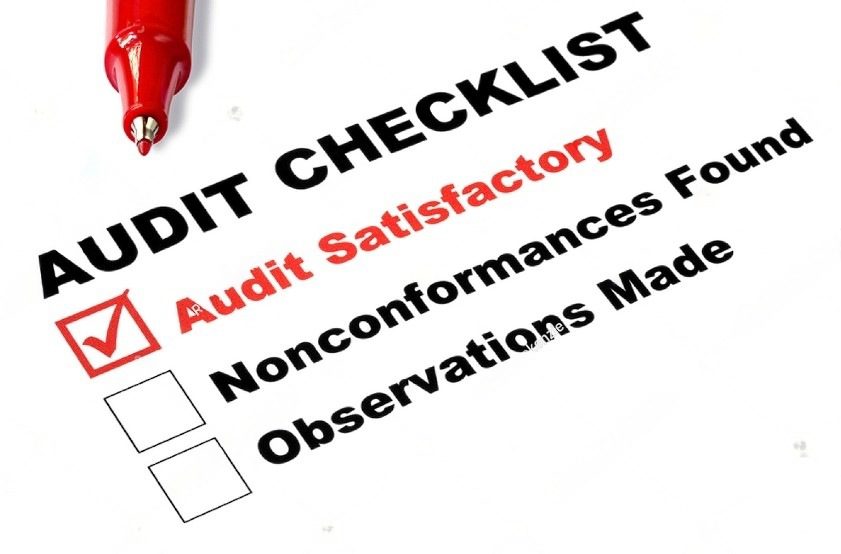
Non-Conformance and How to Minimize It
Let’s have a look at some of the worldwide standards for quality management systems (QMS). The quality management system (QMS) is a collection of resources, assets, processes, and cultural values whose goal is organizational efficiency and customer satisfaction.
ISO 9001:2015: ISO is an abbreviation for “International Organization for Standardization.” It is a non-governmental organization based in Geneva, Switzerland, whose mission is to set voluntary standards for the maintenance of product safety and quality. The framework for quality improvement is provided by ISO 9001:2015. Any firm that delivers services and products (such as the pharmaceutical industry) can implement this standard and thereby very efficiently match customers’ requirements and expectations.
ISO 13485:2016: This ISO standard emphasizes the requirements for a quality management system (QMS) for the design and development of medical devices and related services in accordance with regulatory standards.
FDA 21 CFR Part 820: Under FDA regulations, all device manufacturers who distribute commercial medical devices in the United States of America must comply with FDA 21 CFR Part 820. This document, commonly known as quality system regulation (QSR), outlines Current Good Manufacturing Practice (cGMP) rules.
What Are the Various Types of Nonconformances?
Non-conformances are often classified as minor or major by internal auditors or issuers. However, it should be emphasized that the above-mentioned quality criteria do not need this.
Minor non-conformances and major non-conformances are the two sorts of non-conformances. The difference is the number of corrective measures required to bring your organization back on track.
Regardless of the sort of nonconformance, two points must be made.
Address the nonconformity right away.
Minor nonconformities might escalate into major non-conformities. So, don’t sweep little issues under the rug!
Examining the incidence, detection, and impact of a nonconformance is an excellent means of determining if it is minor or major.
Will the problem reoccur frequently?
Will the system notice the problem in a timely manner?
What are the consequences if the problem is not resolved?
Minor Non-Compliance
A minor non-conformance is one that occurs infrequently, is easily recognized, and has a little direct impact on your consumers.
Minor nonconformities include the following:
- A single document is missing or unsigned.
- Any unlawful change to a document
- Purchase orders are released without prior permission.
- Using equipment after it has passed its calibration date
- Significant Non-Compliance
- If a serious non-conformance is not remedied, it recurs, is difficult to identify, and has a negative impact on your customers.
Major nonconformities include the following:
- Several documents are missing or unsigned.
- Several improper document changes
- Multiple requirement breaches
- Problems that have a negative impact on procedures or operations
How are Non-Conformances Found?
Non-conformances can be identified through internal and external audits, routine testing, product, and protocol inspections, and negative customer feedback.
When a non-conformance is discovered, a non-conformance report (NCR) is created to resolve the issue.
How Are Non-Compliances Handled?
An NCR is primarily used to address nonconformances. The NCR’s primary goal is to state the problem precisely, simply, and rationally. This will assist the organization’s management in implementing necessary adjustments.
Corrective and Preventive Action (CAPA) is a series of measures aimed at improving the organization’s processes and protocols by eliminating non-conformances. Such CAPAs are commonly utilized in the life sciences industries, such as construction industries, medical devices, biotechnology, pharmaceuticals, biologics, and food and beverages.
The CAPA process consists of several steps that must be successfully performed. Each step is meticulously documented in order to ensure continual quality improvement. CAPAs must be carried out correctly in accordance with ISO 9001:2015, ISO 13485:2016, and FDA 21 CFR 820 QMS.
Consider how nonconformances can be addressed in the life sciences industry. You notice that a specific component is not working properly during the production process. You decide to have the provider replace the component.
However, the issue reoccurs, and you initiate a CAPA utilizing the CAPA form to determine the root cause. You discover that the component is built of the incorrect alloy and is insufficient for your needs. You then negotiate the component specs with the supplier to verify that they offer the necessary components.
In this case, a digital tool like SimplerQMS’s CAPA Management Software would be extremely valuable. It offers a ready-to-use, closed-loop CAPA process that is connected with other quality management system procedures and stores everything in a centralized area. With such a system, you can easily discover, uncover, address, and report all preventative and corrective actions (CAPAs) and link them to NCs, audit results, and so on. This gives you a better picture of the status of your CAPAs and issues.
How Can Non-Conformances Be Prevented or Reduced?
Consider another example of a non-conformance and how it might be avoided or mitigated.
The internal audit team at your medical device company discovered that a finished product is defective and does not meet industry standards, i.e., it is non-conforming. For example, during the procedure, a catheter that should fit within a 5 French Guide does not fit properly. This is a significant nonconformance that will have a significant impact on its operation.
Every company will have to deal with nonconformances at some point. It is critical to have an efficient mechanism in place to deal with non-conformances. A thorough management review, review with the affected personnel, conducting an internal audit, documentation and implementation, feedback, and a focus on always improving one’s standards are all required.
The following are the most critical elements in this process:
- Containment
- Immediate corrective action is required.
- Root cause investigation
- Long-term remedial measures
- Validating the approach’s effectiveness
- Containment
You must reply swiftly to the nonconformance. This could be accomplished by immediately warning the customer, separating an item, or reviewing a protocol.
Immediate Corrective Action is required.
Here, you will map out the procedures required to bring the process or product back into compliance.
For each assignment, you will assign responsibilities, timeframes, and tangible proofs.
Analysis of the Root Causes
The root cause analysis provides a response to the question, ‘How did the non-conformance occur in the first place?’ This is a critical stage. Long-term solutions cannot be achieved unless the cause(s) of the nonconformance is identified. The root cause analysis must be factual and answer all queries.
Long-Term Remedial Action
Do not proceed with this step unless you have determined the core cause of the non-conformance.
This stage, like the immediate corrective action step, involves assigning duties, timeframes, methodology used, and provable proofs.
Validating the Approach’s Effectiveness
If the non-conformance is not repeated, the entire technique is proven to be effective. In this final phase, go over all of the records and documents that were used in the previous steps.
Let us return to the example from the section to see how we can minimize/prevent this from happening again.
Containment: Use a unique ‘HOLD’ label to quarantine the items from the supplied batch and move them to a pre-defined holding location under the observation of quality assurance.
Immediate corrective action is required: Delegate responsibility for determining whether one or more batches of the product are non-conforming. Also, whether any of these damaged products were shipped. If this is the case, these items must be returned to the buyer as soon as feasible.
Analysis of the underlying causes: Request that the Quality Assurance (QA) department assess the non-conformance and generate an NCR outlining the reasons for the non-conformance.
Long-term remedial measures: Form a technical team to explore the root reasons for the finished product’s non-conformance. Determine if the product can be re-graded or rejected based on the investigation’s results. Because this is a major non-conformance, the entire batch must be discarded.
Validating efficiency: Check the full procedure again. The items are properly tested over a set length of time. If the non-conformance does not reoccur, it shows that the corrective action was effective.
The Value of Digital Tools Such as Non-Conformance Management Software
Organizations today want a non-conformance management solution that is inventive, upgradeable, and flexible. A solution of this type should be able to meet the needs of your organization while also ensuring compliance with industry standards, product safety, and quality. Digital technologies such as non-conformance management software are examples of such solutions.
QMS Non-Conformance Management Software meets ISO 9001:2015, ISO 13485:2016, and FDA 21 CFR Part 820 QMS requirements.
The software enables continuous monitoring of the present status of nonconformance(s), as well as traceability of components, equipment, suppliers, and CAPAs. You can easily discover, evaluate, and manage nonconformances with the software.
Conclusion-Nonconformance Reports NCRs in Construction Industry
In conclusion, Nonconformance Reports (NCRs) are a critical aspect of quality control in the construction industry. They help identify areas of work that do not meet quality standards or specifications and describe the corrective action needed to prevent such issues from happening again.
Managing NCRs involves a systematic approach that includes marking, controlling, documenting, selecting a position, implementing corrective action, reinspecting, and prevention. Regularly generating high-quality results will boost clients’ confidence in construction firms, as they demonstrate their commitment to strictly limiting specification deviations until adequate resolutions are found.
Construction firms must continuously search for ways to improve quality and prevent similar issues in the future by examining the company’s quality performance and client feedback, incorporating frequent training, and identifying the root causes of nonconformances.
Main Points | Details |
---|---|
Definition of Nonconformance Report (NCR) | A document that deals with work that doesn’t adhere to quality standards or specifications. It describes the issue, how it happened, and how to keep it from happening again. The NCR can also be used to reach an agreement with the customer and record any subsequent corrective modifications. |
Contents of an NCR | Significant parties in the NCR and the standards impacted, description of corrective action implemented or required, steps to ensure that the issue doesn’t arise again, why the work did not conform to the requirements, and what went wrong and the main cause of the NCR. |
7 Steps for Managing Nonconformances in Construction Quality | Step 1: Make a mark; Step 2: Maintaining Control; Step 3: Documentation; Step 4: Selecting a Position; Step 5: Corrective Actions; Step 6: Reinspecting |
tag: # Nonconformance Reports NCRs in Construction Industry