Table of Contents
- Method Statement for Storage Tank Construction
- Reference Codes and Specifications: Construction of a Storage Tank
- Construction Methods for Storage Tanks
- Tank Materials Identification
- Construction and Fabrication of Storage Tanks
- Making Tank Shell Plates
- Making Tank Roof Plates
- Tank Accessories
- Handrails for Storage Tanks and a Spiral Staircase
- Erection of a Storage Tank
- Storage Tank Annular Plate Laying
- Placing the Bottom Plate of a Storage Tank
- Cone Roof Plates and Structures Construction
- Building the Storage Tank Shell
- The Installation of Tank Accessories
Method Statement for Storage Tank Construction
The Method Statement for Storage Tank Construction outlines the steps and regulations for conducting all fabrication, erection, and testing of storage tanks and other related static equipment.
To realize the satisfying completion of the full activities, every task and activity must be completed with the utmost care, with quality workmanship, and in line with the specifications.
This article will provide a reference for an appropriate methodology to realize the activities during a proper tank for the fabrication, erection, and testing of the storage tanks.
Reference Codes and Specifications: Construction of a Storage Tank
- API 650
- IS 803
- ASME Section IX
- ANSI Section V
- Approved Drawing and Specifications
Construction Methods for Storage Tanks
The following sequence describes how the storage tank construction method can be performed:
Tank Materials Identification
Construction and Fabrication of Tanks
- Fabrication of Annular and Bottom Plates
- Shell Plate Fabrication
- Roof Plate Fabrication
- Appurtenances
- Handrail and a spiral staircase
Erection of a Storage Tank
- Laying of an Annular Plate
- Laying the Base Plate
- Cone roof plates and structures construction
- Erection of a Shell Course
- Appurtenances installation
Tank Materials Identification
All components that are required for tank fabrication, such as Plates, Fittings, and other parts of the tankage system, must be properly identifiable by marking heat numbers by hard-punching on each part. Every weld joint needs to be marked with a joint number and a welder number.
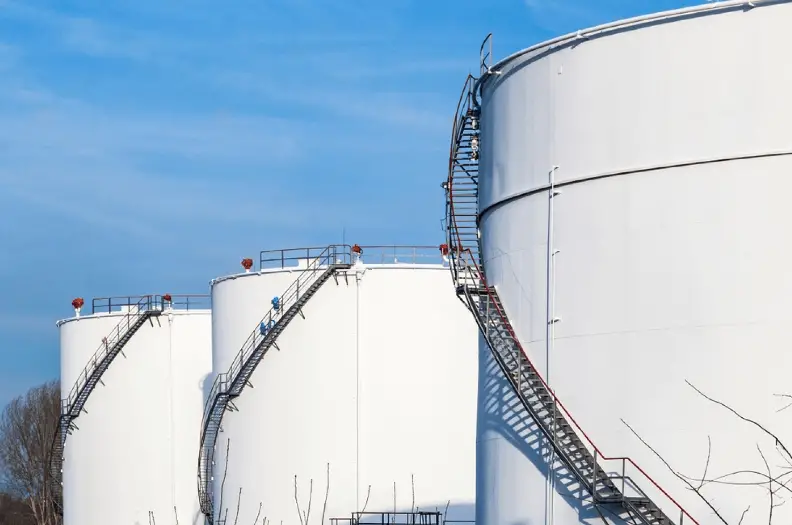
Construction and Fabrication of Storage Tanks
According to the most recent API 650, all fabrication tasks must be performed, such as tank material identification, marking, cutting, rolling, and welding. The craftsmanship must be excellent in every way. With the coordination of the Engineer-In-Charge, it must meet every safety, quality control, and non-destructive testing requirement.
Place all of the plates, structural pieces, and pipelines in a way that permits proper check of the dimensions and heat number.
According to the drawings, label the components.
Fabrication of tank annular and bottom plate
Label the plates according to the drawing.
After a thorough inspection, carry out the cutting operation.
Gas cutting shall administer all cutting activities.
Get rid of the burrs and slag by grinding the cut edges cleanly.
The plates should be stacked in the correct order at designated locations within the fabrication yard.
According to the drawing, the backing strip must be fitted and tacked with an annular plate.
Following completion of fabrication, the underside of the annular and bottom plates must be blast cleaned and painted per the specification to the satisfaction of the Engineer-in-Charge.
As per API 650, check the joint position and root gap for welding after welding inspection.
Making Tank Shell Plates
Lay out all the plates in the space to make cutting and marking easier.
Mark the plates to the satisfaction of the responsible engineer and by the drawing.
The gas-cutting method must be used to execute the cutting process, including beveling, on all four sides.
Grind the cut edges smoothly to get rid of slag and burr.
The plates that have been prepped for stings must be shifted by crane to the rolling area.
The rolling machine must be fed with the plates. using a crane and the appropriate lifting equipment and tackles.
The radius must be checked using a template because the plate must be rolled according to the drawing’s specifications.
The beautiful curvature must be treated with the appropriate care. (5 to 6 mm thick), 36″ long. The template must be used to correctly check rolling curvature.
The inspection authority must check and clear the template plate.
Inspection of the rolled plates is required, and they must be within 3 mm of the tolerance limit.
To hold out the shot blast per the specification, the rolled plates must be shifted to the shot blasting yard.
Before sending for erection, the final profile and dimension check must be administered.
Making Tank Roof Plates
As shown on the drawing, mark the roof plate.
Following clearance from the inspection authority, all cutting operations required by the requirement must be administered.
The gas-cutting method must be administered to all four sides during all cutting operations.
Get rid of the burrs and slag by grinding the cut edges cleanly.
According to the drawing, structural roof components must be fabricated.
To hold up the blasting and painting, these roof plates must be shifted to the blasting yard.
Tank Accessories
Mark the Appurtenances’ specific components by drawing. Following clearance from the inspection authority, all cutting operations required by the requirement must be administered.
By using the gas-cutting method, all cutting operations must be administered.
Get rid of the burrs and slag by grinding the cut edges cleanly.
A suitable cover is placed over the flange face to prevent damage during handling, fabrication, and shipment.
The entirety of the shell nozzle, roof attachments like flanges, flanges at the junction with the pipe, and other requirements, etc. must be fabricated by authorized designs.
Wherever required, all fabrication and welding operations must be carried out after a stage-by-stage inspection.
The NDT specifications follow the code’s criteria.
Handrails for Storage Tanks and a Spiral Staircase
Before marking and cutting, all structural components must be smoothed out.
As shown in the drawing, label the components.
After receiving clearance from the inspection authority, all cutting operations required by the requirement must be administered.
By using the gas-cutting method, all cutting operations must be administered.
Get rid of the burrs and slag by grinding the cut edges cleanly.
Fabrication such as fitting, welding, drilling, etc. must be done by the drawing and only after receiving clearance from the inspection authority.
These structural components must be blasted and painted by the requirement after fabrication.
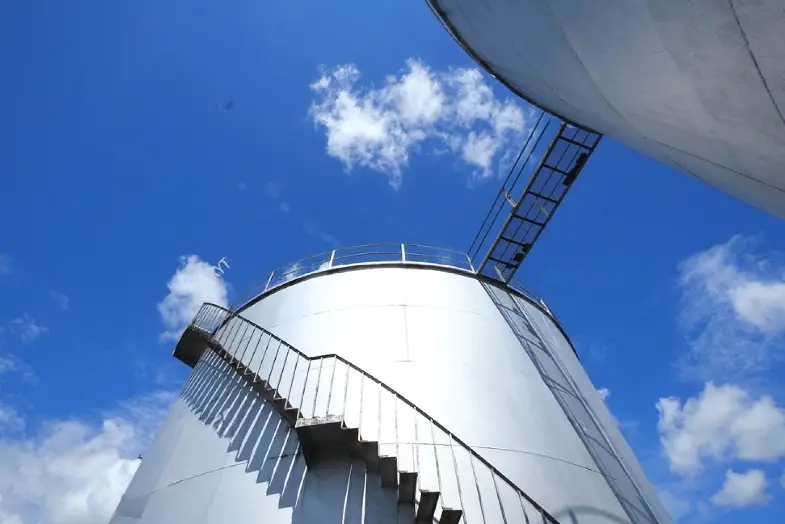
Erection of a Storage Tank
For storage tank erection, there are two methods:
The standard method and the jacking method.
The jacking method for tank erection is employed everywhere since it is easier and safer than the usual method.
Except for the bottom and deck, we compute the entire weight of tank ages when using the jacking method, and jacks are utilized as a result. The weight of the tank that needs to be lifted directly affects how many jacks need to be employed.
Storage Tank Annular Plate Laying
Verify the foundation’s size following clause 8.4.2 of the most recent API 650 specification. Mark the 0 degrees, 90 degrees, 180 degrees, and 270 degrees coordinates on the inspiration from the point of reference after receiving clearance for annular clearance plate laying.
According to the authorized drawing, install the annular plate. To realize the final required radius after weld shrinkage, the annular plate’s out radius must be on the positive side (5 to 10 mm).
The annular plate joint’s orientation must match the approved drawing.
Using the appropriate jigs and fixtures as illustrated in the drawing, fit from the annular plate’s joints must be administered.
The annular plate and backing strip must fit together tightly during assembly.
By welding alternative joints at four quadrants, annular plate joints must be administered.
For welding work in accordance with WPS, qualified welders must be engaged. If a defect is found, it must be removed by grinding, followed by a reweld and the LPT check test.
Until the defect has been cleared, repeat the sequence.
Wire brush and grind the final weld surface after finishing the welding.
Grind the tack after removing the fixtures and jigs that were used to fit the annular joint.
The use of radiography must follow API-650 Sec. 8.
Placing the Bottom Plate of a Storage Tank
As shown in the drawing, place the center plate on the inspiration top.
The center’s coordination allowed for the successive lay of rock bottom plates.
When a short seam and a long seam are fitted according to the drawing, gaps must be maintained.
While the short seam is being fitted and welded, a temporary tack weld must be performed on the Long seam to prevent uneven movements.
To prevent distortion, short seam welding will be administered differently.
Remove the temporary tacks on the Long seam by grinding to facilitate the long seam fit-up after the completion of short seam welding. To prevent distortion, short seam welding will be administered differently.
Remove the temporary tacks on the Long seam by grinding to facilitate the Long seam fit-up after the completion of short seam welding.
While the long seam is being fitted according to the approved drawing, a minimum number of laps must be maintained.
Wherever necessary, joggling shall be administered by pounding. (Triple junction of plates.)
To prevent distortion, channels must be tacked along the long seam before welding can begin. Long seam welding will be administered as an option after shot seam welding’s completion to prevent distortion. Welding must be performed in accordance with the approved WPS and a qualified welder must be engaged.
After welding is finished, the weld joint should be carefully cleaned using wire brooms and grinding.
Only after welding the shell-to-bottom junction shall the sketch to the annular plate joint be welded.
According to the approved process and code specifications, all rock bottom plate joints vacuum box tests must be administered.
If a defect is found during the grind, it must be removed by grinding, rewelding, and conducting the vacuum box test. Until the defect has been cleared, repeat the sequence.
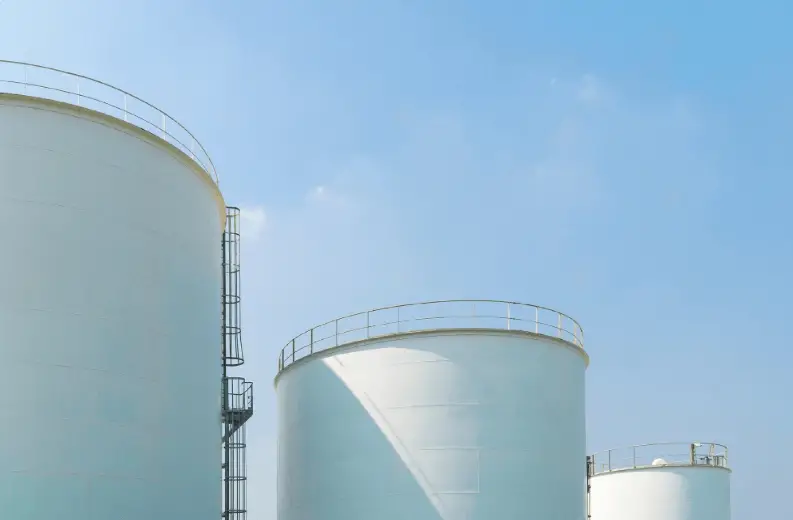
Cone Roof Plates and Structures Construction
Erection, fit-up, welding, and curb ring fit & welding must be completed following the completion of the highest two shell classes.
Install the roof truss, cross girders, and fabricated center drum as shown on the drawing.
Complete the roof structure’s welding using authorized welders and in accordance with authorized WPS. As shown in the drawing, erect the framework and place the roof plates on top. While fitting, both short and long seams on the lap must be maintained following the drawing.
Weld the short seams by using the alternative joint or sequence shown in the drawing to stop the distortion.
Weld the joints in the sequence shown on the drawing and provide adequate support along the length of the long seam.
The fit-up and welding of the roof and top shell nozzles must be done per the approved drawing, which must then be compared to the priority piping drawing.
Building the Storage Tank Shell
Mark the tank’s inner radius on the bottom plates following the completion of the welding of the annular plates and bottom plates.
Attach 25 sets of erection tools to the annular plates at evenly spaced intervals, then transfer the inside tank diameter to the stools.
By the usual method, the final two shell courses must be erected.
The jacking method must be used to build balance shell courses.
By employing a crane, the rolled shell plates must be shifted to the tank foundation area and tacked around the edge.
When handling the rolled plates, due care must be exercised.
It must be carefully ensured that the shell plate is erected to the annular plate’s marked diameter. The shell plates must be aligned using jigs and fixtures.
Complete the fit-up, except the final junction, which must be fitted and welded after the completion of the fitting of the other joints. (To prevent shrinking.
Using a sweep board that is 36″ long, peaking must be checked at the top, middle, and bottom of the vertical joints. Plumpness must be within the tolerance (tolerance 1/200 of the total shell height) and be checked for the verticality of the shell course every 60 degrees.
At regular intervals (3 to 5 meters) inside the shell course, channels must be provided for perfect verticality. By providing the channels, the shell course alignment is facilitated.
The fitted vertical joints’ tack welds must be smoothed down. Offer for inspection and get clearance from the responsible engineer for the vertical fit-up. Complete the primary side welding using qualified welders.
Care must be taken when welding to prevent peaking, which leads to roundness distortion.
The back chip for sound metal from the other side of the weld must be administered after the completion of the first welding.
Before starting the welding, back-chipped grooves must be examined for inspection.
Utilize qualified welders to finish the second side of welding.
On both sides of the weld joint, the joint number and welder number must be marked.
Peaking and distortion due to roundness must be avoided. Wire sweeping and grinding will thoroughly clean the weld joints on both sides. Remove all of the temporary fixtures and jigs, then grind and flush grind the tacks after welding completion on each side. Do the weld refill where required, and M.P.T. will check that area.
Check the radius, circumference, and plumpness to the satisfaction of the engineer in charge, then offer for inspection. Spacers that are 3 mm thick should be kept between the shell courses while installing the following coarse courses.
To align and hold the final shell in a vertical position, erection channels must be attached between the jacked shell and course plates that will be erected at regular intervals.
Using a sweep board that is 36′′ wide, check the peak at the vertical joints of the shell; the permissible tolerance must follow API-650.
After receiving clearance from the responsible engineer, weld the final course vertical seam in the side. Back chip and welding must be administered in the same way as for other shell courses for the engineer-in-charge’s satisfaction.
Following completion of welding, weld visual, verticality, and circumference must be confirmed and recorded to the satisfaction of the engineer-in-charge. The horizontal seam between the first and second shell courses should be finished.
Verify the verticality of the last shell course; verticality (plumpness) tolerance must adhere to API 650 (maximum plumpness at the highest point of the shell about the shell’s rock bottom shall not exceed 1/200 of the total height of the shell from the top of the last shell to the bottom).
The banding and resulting roundness must be carefully considered while welding. Back-chip must be administered by grinding for the sound metal and to the satisfaction of the Engineer-in-Charge. After finishing the second side of welding, wire brushing, and grinding should be used to fully clean the joint on all sides. To the satisfaction of the Engineer-in-Charge, check the banding and plumpness and record the information using the authorized format.
To the satisfaction of the Engineer-In-Charge, provide weld visuals. Mark the RT locations per the Engineer-in-Charge’s instructions, then complete the RT by API-650 criteria. Offer the RT video to the Engineer-in-Charge for assessment. If any repairs are necessary, they must grind out the sound metal and reweld the repair area by API -650 sec-8 criteria.
Take the repair location to the satisfaction of the Engineer-In-Charge and resubmit your offer for the inspection. The erection of the spiral staircase must be administered following the drawing, including brackets, and without fouling the welds.
Grind out all of the temporary cleats and tacks. If a defect is found, it must be repaired by grinding the defect area for the sound metal plus 150mm from both ends of the defect.
On the repair site, perform the DP test. complete the full process until the repair has been cleared to the Engineer-In-Charge’s satisfaction.
After completion of the side to the bottom out welding, a visual inspection will be administered to the satisfaction of the Engineer-In-Charge.
All undesired materials and scrap must be removed from inside the tank after the shell-to-tank welding and NDT work is completed, as well as after all erection and welding work on the tank in the side related to the roof and tank structure.
Completed RT of the horizontal and vertical joints.
After finishing the Shell to Bottom Welds, a Sketch of the Annular Plate Joint Fit Up must be administered.
For rock bottom plate sketch short seam, long seam, and sketch to annular plate junction, the vacuum box test must be administered. A replacement must be repaired and retested per API-650 and the approved procedure if any repairs are necessary.
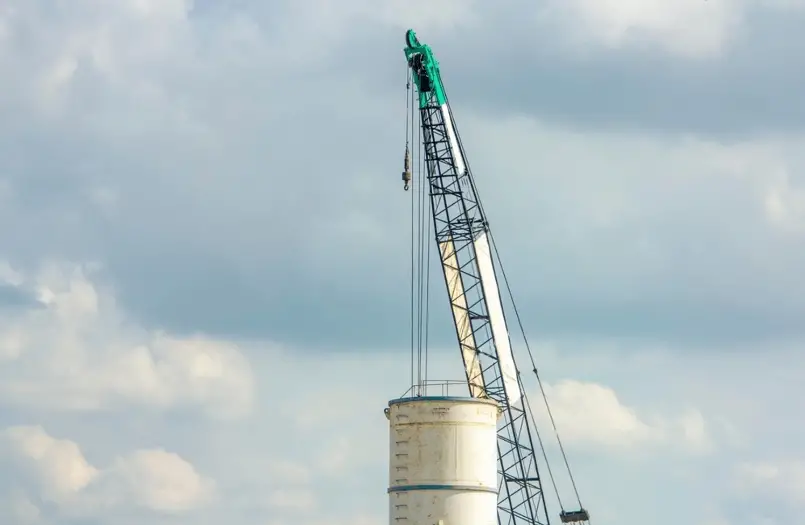
The Installation of Tank Accessories
Before erection, the required NDT must be completed and flanges to pipe joints must be prefabricated.
Using the illustrations as a guide, mark the nozzle’s placement. After satisfactory inspection by inspection authorities, cut the openings with gas cutting.
Install the nozzles per the height and orientation shown in the drawing. Put in RF. Before nozzle erection, wherever required, pads.
To prevent distortion during welding, appropriate fixtures, and jigs must be provided.
For the inspection clearance, orientation, elevation, and projection must be maintained following the drawing and offer. By using jigs and fixtures to prevent distortion, proper care must be given during welding.
The qualified welder must weld following WPS.
The longitudinal joint must be radiographed since the man-Hole neck must be fabricated. Pneumatic testing must be done on every RF Pad weld at a pressure of 1.05 Kg/cm2. To the satisfaction of the responsible engineer, the pneumatic test must be administered.
When all shell nozzles have been successfully welded from all sides, the RF Pad welds must pass visual and LPT inspections to the engineer-in-charge’s satisfaction.
tag: # Method Statement for Storage Tank Construction