Table of Contents
Method of Statement for Pneumatic Testing of Distribution and Process Piping System
Brief Explanation of Pneumatic Testing
Pneumatic testing is a non-destructive test method that is utilized to identify any leaks or damages in the distribution and process piping system. It involves filling the piping system with compressed air and monitoring it for a specific duration to ensure that it can maintain the required pressure without any drops or pressure losses.
The test involves pressurizing the system with air, which simulates actual operating conditions so that any potential problems can be identified before the system is put into operation.
The pneumatic testing method is widely used in various industries due to its accuracy in detecting even small leaks in pipes.
Its sensitivity makes it ideal for use in critical applications such as those found in nuclear power plants, chemical plants, and gas pipeline systems. This testing technique has become an industry standard because of its ability to detect leaks quickly and efficiently.
Importance of Testing Distribution and Process Piping System
The distribution and process piping systems are critical components of most industrial processes. These systems are responsible for transporting liquids, gases, chemicals, and other materials throughout the facility. A malfunction or failure within these systems can result in significant financial loss from production downtime, damage to equipment or facilities, environmental contamination, or even injuries to personnel.
The importance of pneumatic testing cannot be overstated as it helps ensure that pipe systems are operating at optimal levels before they are put into service. It is vital for identifying defects such as cracks, pinholes, or other damages that may lead to leaks after commissioning.
By detecting potential problems before they occur, companies can avoid costly repairs down the line and minimize risks associated with accidents. Pneumatic testing is crucial when commissioning new installations or when performing routine maintenance on existing ones.
It helps ensure safe operation by identifying issues before they turn into costly problems down the line. In the next section, we will delve into the pre-testing preparation that needs to be done before conducting pneumatic testing on distribution and process piping systems.
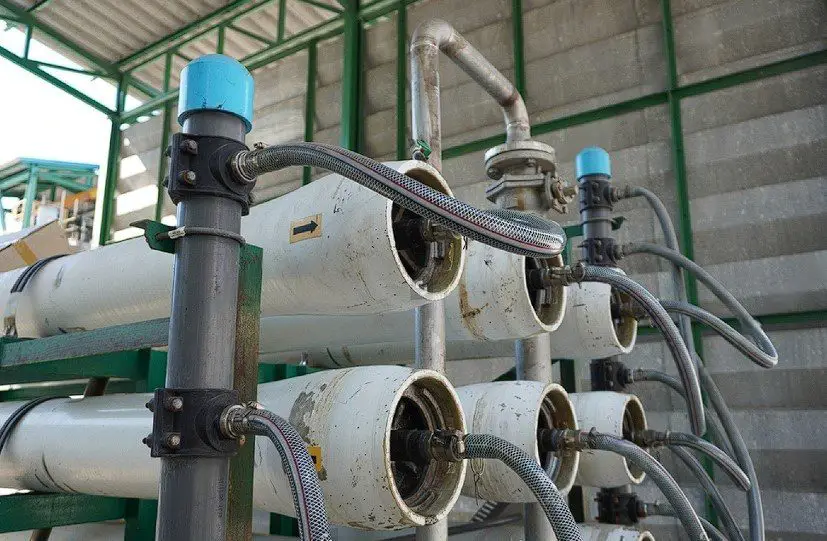
For conducting a pneumatic test, the list of tools and instruments is provided below:
- Air Cylinder
- 6” Manifold with connectors of 12″ and 34″
- Temperature and pressure recorder
- Hand tools
- Pressure relief valve
- Other valves and fittings according to test specifications
- 20 m 1/2 ” air hose
- Pressure gauge set
Pre-Testing Preparation
Safety Precautions to be Taken Before Testing
Before conducting a pneumatic test on a distribution or process piping system, it is important to take necessary safety precautions to avoid any accidents. The following safety measures must be taken before the test: Firstly, ensure that all personnel involved in the testing process are trained and familiar with the procedure.
Before starting the test, conduct a safety briefing and outline the potential hazards and risks involved. Secondly, all of the equipment used for testing must be inspected before usage to ensure they are in good working condition.
This includes checking that pressure gauges, air compressors, and hoses have no visible damage or leaks. Protective gear such as gloves and safety glasses should be worn by personnel who will be exposed to compressed air during testing.
Inspection of the Piping System for Any Damages or Leaks
Before starting a pneumatic test on distribution or process piping systems, an inspection must be carried out on all pipes and fittings. This inspection must identify any damages or leaks present in the system. If any visible damages are found during inspection such as cracks, dents, or corrosion, these must be thoroughly repaired before conducting the pneumatic test.
In cases where there are leaks detected at joints or valves during the inspection, these too need repair. Failure to repair these damages before proceeding with testing may result in dangerous consequences such as explosions which can cause serious injuries as well as property damage.
Identification of Test Pressure and Duration
Before commencing with a pneumatic test of distribution or process piping systems it is crucially important that there is an understanding of what test pressure (expressed in PSI) will be required for each section under scrutiny.
The duration of testing depends upon various factors including pipe thickness, length as well as other variables, and must be agreed upon beforehand. A typical test period lasts for about 30 minutes to an hour.
By identifying the correct test pressure and duration, the pneumatic test can be conducted effectively and objectively, allowing the detection of any leaks or damages in the piping system. It is important to note that these parameters should not exceed safe limits set by applicable codes and standards.
Testing Procedure
Pressure Gauge Installation
Before conducting a pneumatic test on a distribution and process piping system, it is vital to install pressure gauges. Pressure gauges are the primary monitoring tool used during testing and help identify any pressure fluctuations or drops that occur during the test. The gauge should be installed at the highest point of the piping system to ensure accurate readings.
It is important to note that the pressure gauge used for testing should have sufficient capacity to read both low and high-pressure conditions.
A common range for gauges used in pneumatic testing of distribution and process piping systems is between 0-300 psi with an accuracy within ±1%.
After installing the gauge, it is essential to confirm its accuracy by comparing it with another instrument calibrated against a known standard. This step will help ensure that accurate results are obtained during testing.
Filling the System with Compressed Air
Once all necessary preparations have been completed, filling the system with compressed air can begin. Before introducing compressed air into the piping system, all drain valves must be opened while all other valves remain closed. Compressed air should gradually be introduced into the system until reaching a specific test pressure level.
It is recommended that compressed air should be introduced in stages and increments of 10%, allowing time for inspection and monitoring before increasing again. When reaching maximum test pressure, there should be no signs of leaks or damages – such as bulging pipes or broken fittings – which require immediate rectification before proceeding.
Monitoring Pressure for a Specific Duration
The duration of pneumatic testing depends on various factors such as pipe size, length, complexity of layout, and pipe material type. In general terms, however, pneumatic tests are typically conducted within two hours or until reaching a predetermined time set by regulation agencies.
During this time frame, it’s crucial to monitor the pressure gauge readings for any significant changes. Any pressure drop indicates there is a potential leak or damage to the system, requiring immediate inspection before testing can continue.
It is essential to monitor the pressure gauge readings continuously throughout the testing process and record results. At the end of testing, the recorded data should be analyzed, and recommendations made accordingly.
Identifying Any Leaks or Damages During Testing
The final step of a pneumatic test is identifying any leaks or damages in the piping system. This step can be challenging, but it is vital as any leaks or damages can cause severe problems in operation and safety. The first thing to check is pressure gauge readings for significant drops during testing.
If there has been a pressure drop, it indicates there may be leaks or damages within the piping system. Inspect all visible areas of the piping system for leaks; this includes fittings, valves, joints & seams.
If no visible signs are found but still suspect a leak based on gauge readings – employ non-invasive techniques such as pipeline acoustic detection tools (PADS) for accurate results.
Once all areas have been inspected thoroughly and repaired if necessary – another pneumatic test must be conducted until satisfying results are obtained that demonstrate safe operations with sufficient integrity.
Post Testing Procedures
Inspection of the Piping System After the Test
After the completion of the pneumatic testing, it is necessary to inspect the piping system for any damages or leaks that may have occurred during the test. A thorough inspection should be carried out to ensure that any issues are identified and addressed before operating the system.
It is important to note that even if no obvious leaks were identified during testing, there could still be leaks in parts that are not readily visible.
The inspection should start with a visual check of all accessible areas of the piping system. This includes checking for any physical damage to pipes, valves, fittings, or flanges.
It is important to look for signs such as corrosion or deformation on metal pipes and components and soft spots on flexible hoses. Any damages found should be noted down for further action.
Checking for Any Damages or Leaks That May Have Occurred During The Test
To identify any leaks in parts not readily visible, a leak detection solution can be applied at all joints such as flanges and threaded connections. Bubbles forming at these points indicate gas leakage from the joint. The leak detection solution used must be compatible with compressed air and safe to use concerning materials in contact.
If a leak is detected during post-testing inspection, it should be repaired immediately before proceeding further with the operation of the piping system. Rechecking after the repair is essential.
Recording Results and Documenting Findings
The final step in post-testing procedures involves recording results and documenting findings. A detailed report needs to be prepared summarizing actions taken before testing, observations made during testing, results obtained after testing with details such as pressure readings duration, etc., inspections conducted post-test plus test findings including their resolution status.
This documentation provides a reference point for future periods of testing regarding tests completed earlier – useful in identifying recurring issues. It is also important to maintain a record of the pneumatic test report along with associated inspection records and repair reports.
These documents should be maintained for future reference, auditing, and compliance purposes. Proper documentation also helps in tracking the history of the piping system and ensures that safety standards are met to avoid risks that may arise due to any negligence during testing or operation.
Test Records
All parties must sign the Original Piping Pressure Test Report after witnessing the pressure test.
Depressurization
The line must be depressurized by gradually opening the vent valve or depressurizing valve once the test has been successfully completed.
When depressurizing the system, make sure that no surrounding constructed items are damaged by a strong blast of air.
Reinstatement
The Pipe “Post-test Critical Component Reinstatement” must be signed off by all parties involved and all items that were removed for the pneumatic test must be put back.
The Contractors QA/QC Manager must get the signed format.
All instruments must be visually verified and recorded after the reinstatement.
Conclusion
Recap of the importance of pneumatic testing for distribution and process piping systems
The importance of pneumatic testing for distribution and process piping systems cannot be overstated. A leak or damage to a pipeline can lead to catastrophic consequences such as explosion, fire, or environmental damage.
By conducting regular pneumatic tests, potential issues can be identified and addressed before they become major problems.
The testing procedure outlined in this article provides an effective way to ensure the integrity of the piping system. With proper preparation and careful monitoring during the test, leaks and damages can be identified quickly and easily.
Final thoughts on maintaining safe and efficient operations through regular testing
Regular pneumatic testing is an essential component of maintaining safe and efficient operations in any industrial setting that involves distribution or process piping systems. It is important to remember that this type of testing should not be viewed as a one-time event but rather as part of an ongoing maintenance program.
By conducting regular tests at specified intervals, potential issues can be detected early on, minimizing risks to personnel, equipment, and the environment.
Furthermore, addressing issues early on often saves money in repair costs in comparison to repairing damages caused by delayed detection over time. ; with proper preparation and adherence to established procedures outlined in this article, companies can ensure safe operation while extending the useful life expectancy of their pipelines.
tag: # Method of Statement for Pneumatic Testing of Distribution and Process Piping System