Table of Contents
What is the Method Statement for Roadbase Construction?
A method statement for roadbase construction is a detailed document that outlines the step-by-step procedure and guidelines for constructing the roadbase in a specific project. It provides a systematic approach to ensure the successful installation of the roadbase layer, which serves as the stable foundation for the road pavement above.
Objective
The objective of this method statement is to outline the procedures and techniques to be employed for the placement of subbase and roadbase materials.
Construction Method
The construction process will follow the sequence of activities outlined below:
Placing of Lower Subbase
The underlying subgrade will be prepared and compacted in accordance with the specified requirements before placing any Lower Subbase material.
Lower Subbase material will be placed over the entire width of the formation in one or more layers, with each layer not exceeding 200mm of compacted thickness, as indicated in the drawings.
Moisture content in each layer of Lower Subbase will be adjusted as necessary to achieve uniformity throughout the material suitable for compaction.
The Lower Subbase will be compacted using approved compaction equipment to achieve at least 95% of the maximum dry density determined by the B.S. 1377 Compaction Test (4.5 km rammer method).
The final top surface of Lower Subbase will be shaped to the required thickness, shape, superelevation, levels, and grades as specified in the drawings and within the tolerances defined in the specifications.
Regular level checks will be conducted using control/dipping pegs along both sides of the pavement during construction.
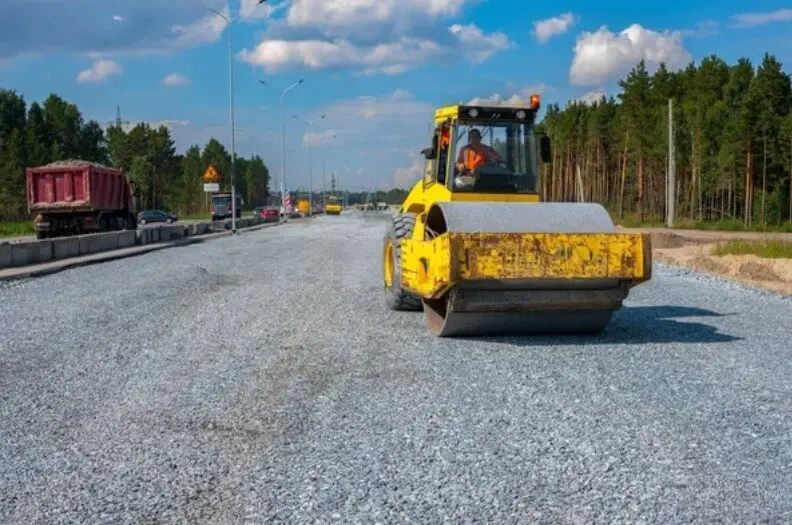
Placing of Upper Subbase
The underlying subgrade or subbase will be prepared and compacted as per specifications before placing any upper subbase material.
Crushed aggregate from approved sources will be placed over the full width in one or more layers, with each layer not exceeding 200mm of compacted thickness, as indicated in the drawings.
Moisture content in each layer of upper subbase will be adjusted as necessary for proper compaction, and a water truck will be used to maintain the correct moisture level.
The upper subbase will be compacted using suitable compaction equipment to achieve at least 95% of the maximum dry density determined by the B.S. 1377 Compaction Test (4.5 km rammer method).
Care will be taken to maintain a uniform gradation of the materials and prevent segregation into coarse and fine parts during compaction.
The final top surface of Upper Subbase will be shaped to the required thickness, shape, superelevation, levels, and grades as specified in the drawings and within the tolerances defined in the specifications.
Regular level checks using control/dipping pegs will be conducted along both sides of the pavement. Additionally, a joint survey will be performed on the existing road profile level to establish the original profile of the location being overlaid.
Placing of Road Base or Wet Mix Macadam
Approved machinery will be used for laying the material in layers and compacting it in accordance with specifications. Any areas with loose surfaces or deficiencies in fines due to segregation will be rectified by removing and replacing them with properly graded material.
The preparation of Road Base and Wet Mix Macadam will follow the procedures of the previous layers.
Before laying, the survey team will set out the string line for the grade line sensor at regular intervals along the sides of the carriageway, ensuring it is set to the required levels.
After jointly surveying the stringline level, the laying operations may commence, ensuring that all gradeline and slope sensors are properly set and functional.
This might interest you: Method Statement for Road Marking Installation
Plant and Equipment
The required machinery includes:
Motor Grader/paver
Back pusher with power broom
Compaction equipment (rollers)
Water truck
Surveying equipment (level, theodolite, etc.)
Quality Control and Safety
Conduct regular quality control tests on roadbase materials and compaction to ensure compliance with project specifications.
Follow all safety protocols and measures to protect workers and the public during construction activities.
Monitor the construction process closely to ensure adherence to the method statement and the project’s quality and safety standards.
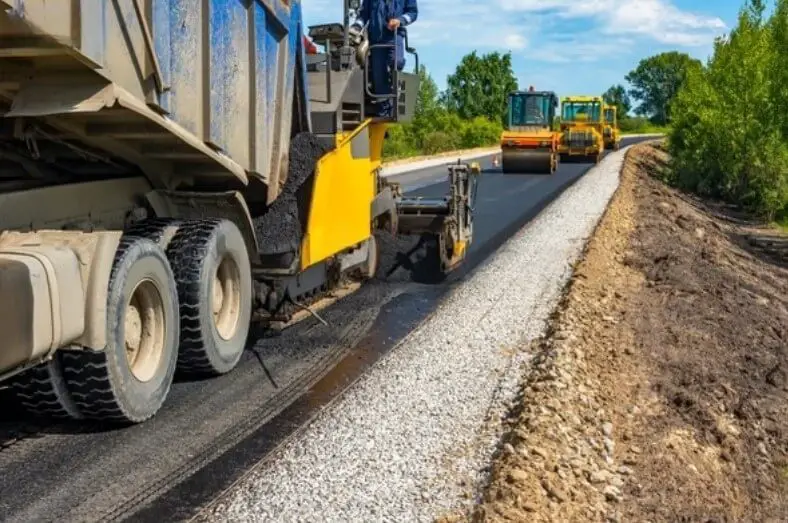
Environmental Considerations
Implement measures to mitigate any potential environmental impact during roadbase construction, such as dust suppression and proper waste management.
Record Keeping
Maintain detailed records of construction activities, quality control tests, and any deviations from the method statement for future reference and documentation.
tag: # Method Statement for Roadbase Construction