Table of Contents
- What is the Method Statement for Gas Purging?
- Introduction
- Purpose of Gas Purging
- Scope of Gas Purging
- References for Gas Purging
- Responsibilities in Gas Purging
- Manpower for Gas Purging
- Tools and Equipment for Gas Purging
- Methodology of Gas Purging
- Quality Control and Inspection
- Safety Instructions and Precautions
- Wrapping Up
What is the Method Statement for Gas Purging?
The Method Statement for Gas Purging serves as a guideline for carrying out nitrogen purging works in various settings such as buildings, plants, and refineries. It covers all mechanical equipment that requires preservation by nitrogen purging. The process involves using nitrogen to displace other gases within a system or piece of equipment, ensuring safety and preventing risks such as combustion or corrosion. The method statement includes a safe work procedure and control measures, which can be edited and added to suit specific project details. It also ensures that all safety requirements are adequately addressed and the work is carried out in accordance with industry standards.
Introduction
Gas purging, a critical procedure in various industries, involves the removal of harmful or undesirable gases from pipelines, vessels, or other industrial installations. This process is typically achieved by introducing an inert gas into the system to displace the unwanted gas, ensuring safety and operational efficiency.
The importance of gas purging cannot be overstated. In industries such as oil and gas, chemical manufacturing, and HVAC, gas purging is essential for maintaining safe working conditions and preventing potential hazards. For instance, in the oil and gas sector, gas purging can prevent the risk of explosions by removing flammable gases from pipelines and storage tanks. Similarly, in HVAC systems, purging helps remove air and non-condensable gases, improving the efficiency and longevity of the system.
In essence, gas purging plays a pivotal role in ensuring the safety, efficiency, and reliability of various industrial operations. As we delve deeper into the method statement for gas purging, we will explore its procedures, safety measures, and best practices in more detail.
Purpose of Gas Purging
Gas purging serves a critical role in various industrial processes, particularly in the context of buildings, plants, and refineries. The primary objective of gas purging is to ensure safety and maintain the integrity of equipment and systems. It involves the removal of unwanted gases or substances from pipelines, vessels, and other types of industrial equipment. This process is crucial in preventing potential hazards that may arise due to the presence of flammable or harmful gases.
Moreover, gas purging is not just about safety; it’s also about preservation. Specifically, nitrogen purging has become a standard practice in many industries. Nitrogen is an inert gas, meaning it does not react with other substances easily. This property makes it an excellent choice for preservation purposes. When nitrogen is used to purge systems in buildings, plants, and refineries, it displaces oxygen and other gases, thereby preventing oxidation and other chemical reactions that could degrade the system’s components.
This practice helps prolong the lifespan of the equipment, reduces maintenance costs, and ensures the smooth operation of industrial processes. Thus, the need for preservation by nitrogen purging is both a practical and economic consideration for many industries.
Scope of Gas Purging
Gas purging is a vital process in the maintenance and preservation of various types of mechanical equipment. It plays a significant role in ensuring the safety, efficiency, and longevity of these systems.
The Process
The process of gas purging involves the use of an inert gas, typically nitrogen, to displace other gases within a system or piece of equipment. This displacement is crucial as it helps to prevent the risk of combustion, corrosion, or other forms of damage that could be caused by the presence of oxygen or other reactive gases. The purging process is meticulously controlled and monitored to ensure that it is carried out safely and effectively.
Applications
The scope of gas purging is extensive, with applications in a wide range of industries and settings. These include, but are not limited to:
- Oil and Gas Installations: In the oil and gas industry, gas purging is used to ensure the safety and integrity of pipelines, storage tanks, and other equipment. It helps to prevent the risk of explosions and other accidents that could be caused by the presence of flammable gases.
- Chemical Plants: Chemical plants often deal with a variety of volatile and potentially dangerous substances. Gas purging is used to ensure that these substances are handled safely, reducing the risk of chemical reactions that could lead to accidents or damage to equipment.
- Power Generation Facilities: In power generation facilities, gas purging is used to maintain the integrity of turbines, boilers, and other equipment. It helps to prevent corrosion and other forms of damage that could impact the efficiency and lifespan of these systems.
References for Gas Purging
There are numerous references and guidelines related to gas purging. These include industry standards, safety regulations, and technical manuals. These documents provide valuable insights and instructions on how to carry out gas purging safely and effectively.
Responsibilities in Gas Purging
The successful execution of gas purging requires the involvement of various personnel, each with their specific roles and responsibilities. The site manager oversees the entire operation, while the construction manager ensures that all physical aspects of the project are carried out correctly. The quality control inspector is responsible for monitoring the process and verifying compliance with standards. The mechanical supervisor oversees the technical aspects, and the safety officer ensures that all safety procedures are followed.
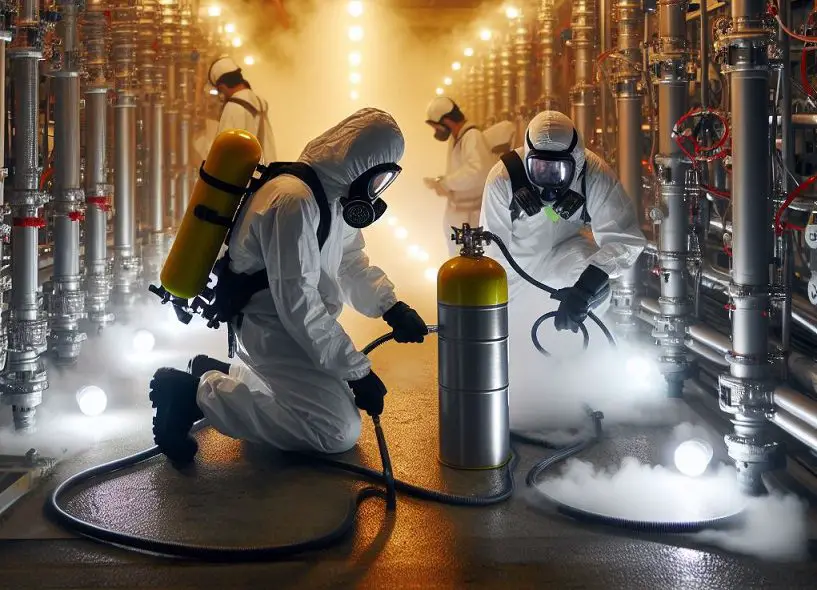
Manpower for Gas Purging
Gas purging, a critical operation in various industries, requires a team of skilled professionals. The manpower involved in this process is diverse, each with their specific roles and responsibilities.
Roles and Responsibilities
Mechanical Foreman: The mechanical foreman supervises the entire operation. They are responsible for coordinating the team, ensuring that everyone understands their roles, and that the work is carried out safely and efficiently.
Mechanical Fitters and Pipe Fitters: These professionals are at the heart of the purging process. Mechanical fitters and pipe fitters perform the actual purging, ensuring that the gas is properly and safely removed from the system.
Forklift or Crane Operator: The forklift or crane operator is responsible for handling the equipment used in the purging process. This includes moving heavy cylinders of gas and other equipment to and from the work area.
Riggers and Scaffolders: Riggers and scaffolders play a crucial role in ensuring safe access to the work area. They set up scaffolding and other structures that allow the team to reach the areas where purging is needed.
Importance of Teamwork
The success of the gas purging process relies heavily on the teamwork of these professionals. Each member of the team must perform their role effectively and work together to ensure the safety and efficiency of the operation. Regular training and communication are key to maintaining a high-performing team.
Tools and Equipment for Gas Purging
Gas purging, a critical process in various industries, requires a range of specialized tools and equipment. The selection and maintenance of these tools are crucial to the safety and effectiveness of the purging process.
Variety of Tools and Equipment
The tools and equipment used in gas purging are diverse, each serving a specific purpose in the process. These include:
Purging Devices: These devices control the flow of gas during the purging process. They are designed to ensure that the correct amount of gas is used, minimizing waste and ensuring efficiency.
Nitrogen Cylinders: Nitrogen is often used in gas purging due to its inert properties. Nitrogen cylinders store this gas under pressure, ready for use when needed.
Pressure Gauges: These tools measure the pressure of the gas being used in the purging process. They help ensure that the gas is at the correct pressure, which is vital for the process’s effectiveness.
Hoses: Hoses are used to transport the gas from the storage cylinders to the area being purged. They must be durable and resistant to the gas being used.
Importance of Good Condition
Ensuring that all tools and equipment are in good condition is crucial. Tools in poor condition can lead to inefficiencies in the purging process, or worse, safety hazards. Regular inspections and maintenance are necessary to keep the tools in optimal condition. This includes checking for any signs of wear and tear, ensuring that pressure gauges are accurate, and that hoses are free from leaks.
Methodology of Gas Purging
Gas purging is a critical process in various industries, including construction, manufacturing, and refining. It involves a systematic procedure to ensure the safety and efficiency of equipment and systems.
Isolation of System or Equipment
The first step in the gas purging process is the isolation of the system or equipment to be purged. This involves shutting off all connections to the system, ensuring that no external gases or substances can enter during the purging process. The isolation step is crucial to maintain the integrity of the system and prevent any potential contamination.
Introduction of Nitrogen
Once the system is isolated, the next step is the introduction of nitrogen. Nitrogen is commonly used in gas purging due to its inert properties, meaning it does not react with other substances. The nitrogen displaces the existing gas or air within the system, effectively “purging” it of any unwanted substances.
Achieving Desired Purity Level
The introduction of nitrogen continues until the desired purity level is achieved. This level varies depending on the specific requirements of the system or equipment. The purity level is often determined by measuring the oxygen content within the system, with a lower oxygen content indicating a higher level of purity.
Application in Various Settings
The methodology of gas purging is applicable in various settings. In buildings, it can be used to purge air conditioning and heating systems. In plants and refineries, gas purging is often used to prepare pipes and vessels for use, ensuring they are free from potentially harmful gases before operation.
Gas purging is a vital process that ensures the safety and efficiency of systems and equipment across various industries. By following a step-by-step procedure, it allows for the effective removal of unwanted gases, ensuring the optimal performance of the system or equipment.
Quality Control and Inspection
Quality control and inspection are integral components of the gas purging process, ensuring that the procedure is executed correctly and efficiently.
Role of Quality Control and Inspection
Quality control and inspection serve a vital function in gas purging. They act as the gatekeepers of the process, ensuring that each step is carried out according to established standards and protocols. This involves checking the equipment, monitoring the introduction of nitrogen, and verifying the achieved purity level. These steps are crucial in ensuring that the desired outcomes of the gas purging process are achieved.
Daily Monitoring and Compliance Verification
The quality control inspector plays a pivotal role in the gas purging process. Their primary responsibility is to monitor the daily activities associated with gas purging. This includes overseeing the isolation of the system or equipment, the introduction of nitrogen, and the achievement of the desired purity level.
In addition to daily monitoring, the quality control inspector is also responsible for verifying compliance with the method statement. The method statement is a document that outlines the procedure for gas purging, detailing each step that needs to be taken. The inspector ensures that the process aligns with this statement, checking for any deviations and addressing them promptly.
Quality control and inspection are essential aspects of gas purging. They ensure that the process is carried out correctly, efficiently, and safely. By monitoring daily activities and verifying compliance with the method statement, the quality control inspector plays a crucial role in maintaining the integrity of the gas purging process.
Safety Instructions and Precautions
In the realm of gas purging, safety is not just a priority, but a paramount concern. The process involves handling potentially hazardous materials, and as such, it necessitates stringent safety measures.
Importance of Safety Measures
All personnel involved in the gas purging process must adhere to a set of safety measures. These measures are designed to protect the workers from potential hazards and to ensure the smooth execution of the process. They include the use of appropriate personal protective equipment (PPE), such as gloves, safety glasses, and protective clothing. This equipment serves as the first line of defense against potential exposure to harmful substances.
In addition to PPE, adherence to safe work practices is also crucial. These practices include proper handling and storage of materials, correct operation of equipment, and observance of safety protocols during the purging process. These practices help to minimize the risk of accidents and ensure the safety of all personnel involved.
Role of the Safety Officer
The safety officer plays a crucial role in ensuring the implementation of these safety procedures. Their responsibilities include monitoring the work environment for potential hazards, enforcing safety regulations, and providing safety training to personnel. They are also responsible for conducting regular safety inspections to ensure that all safety measures are being followed.
The safety officer’s role extends beyond mere enforcement. They also play a key role in fostering a culture of safety within the organization. By promoting awareness and understanding of safety measures, they help to ensure that safety becomes a shared responsibility among all personnel.
Wrapping Up
In conclusion, gas purging is a critical process in various industries. It requires careful planning, competent manpower, appropriate tools and equipment, and strict adherence to safety procedures. By following the correct method statement for gas purging, we can ensure the safety and longevity of our equipment and facilities.
tag: # Method Statement for Gas Purging