What is the Method Statement for Expansion Joint?
A Method Statement for Expansion Joint outlines the procedures and steps that will be followed to install, maintain, or replace expansion joints in a construction project.
Expansion joints are critical components that allow structures to accommodate movements caused by temperature variations, settlement, seismic activity, and other factors.
Purpose
This procedure covers the work method for providing & fixing extruded aluminum plates, filler board for expansion joints between column, beam, slab and walls etc. of thickness 50mm & 100mm as per the drawings & specifications.
Table of Contents
Scope
The scope covers the work method for surface preparation, fixing of extruded aluminum
plates, fixing of filler boards, cleaning etc.
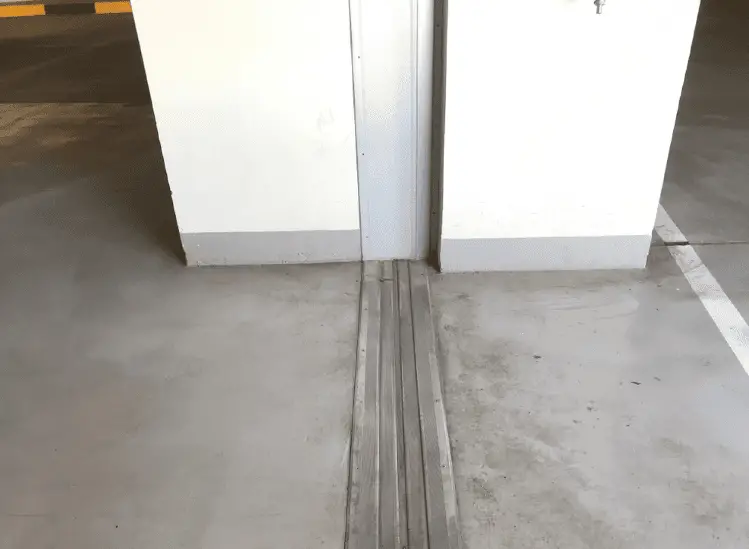
Reference Standards
- Contract Specification/BOQ
- Approved Architectural Drawing
- IS: 183 8 Part-1 Specification for performed fillers for expansion joint in concrete pavements and structures (non-extruding & resilient type) part 1 Bitumen impregnated fiber.
- DIN 18540 Sealing of exterior wall joints ID Building construction using joint sealant-design of joints.
- DIN 52455 Testing of sealing compounds ID building construction-Adhesion & Expansion test.
- DIN 52458 Testing of Sealing compound ID Building construction – Determination of Recovery.
Materials
Filler boards: Expansion Joint Filler board is a pre-moulded, high performance joint filler board. It is a closed cell and of cross linked structure. It has an excellent recovery.
Joint Adhesive: The joint/tape adhesive shall be solvent-free, thixotrophic two part epoxy based adhesive suitable for bonding the joint tape/stripe to different substrates.
Responsibility
The Project Manager shall be responsible for all the activities of work execution.
The Site Engineer shall be the responsible to execute the joint treatment work accordance with the method statement.
The Surveyor shall be responsible for the level and coordinate checking with respect to the drawing. Work with site engineer to carry out the as- built survey/ top of concrete if any.
The QC Engineer shall be responsible for ensuring the quality of the expansion joint materials & correct application as per manufacturer recommendations.
The Safety Officer shall be responsible to ensure the safety of workers during the execution of the work.
Procedure
Remove dust, flakes or foreign particles by jet of dry air to clean the surface.
Cut filler board of approved make of appropriate width from the desired sizes and place the same in the groove in a way to flush with the external surface except for space required for sealant.
Filler board shall be placed at the side and held tight with the concrete surface by suitable means.
Care shall be taken that the boards do not get damaged or warped during all the operation. Utmost care shall also be taken to ensure that the board is held tightly to the concrete surface and no stone chip, concrete etc. is allowed to splash between the board and the existing concrete surface against which the board is placed.
In case of the new casting joint filler board of appropriate width is fixed with copper screws before pouring concrete.
The width is designed to flush with the external surface except for space for application of sealants.
After the deshuttering, the surface shall be cleaned off all grit, mortar, cement plaster etc. The surface shall be made dry, free from grease and dust.
In case of roof the expansion joint in beams placed vertically, shall be extended upwards, when RC/Brick masonry curbing is laid to the desired height(approximately 450mm) over which horizontal flat board is laid to the extent of 150mm or so as shown in drawing as per procedure laid down here in before.
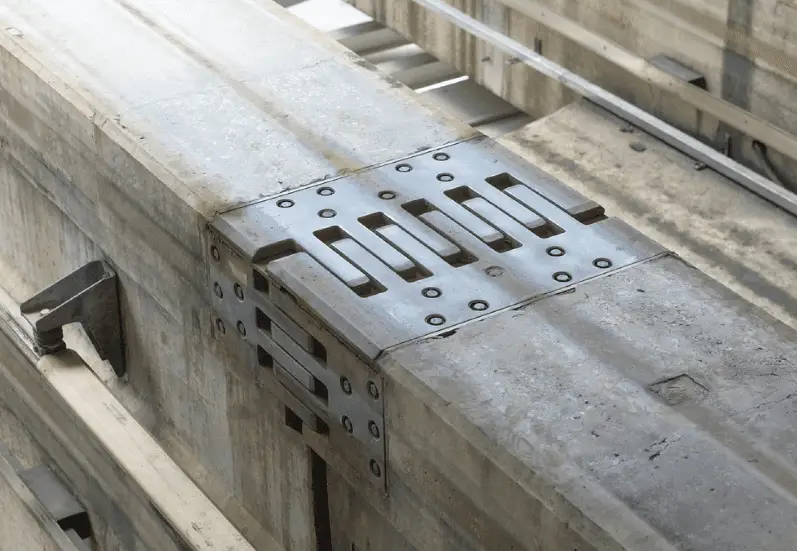
Documentation
- Request for Inspection (RFI)
- Level Sheet
- Technical Data Sheets for Expansion Joint Filler Board
tag: # method statement for expansion joint