Table of Contents
What is Plate Load Test Method Statement?
The plate load test method statement is a description that ensures necessary precautions, health & safety risks have been identified and safety systems are put in place during the testing activity in determining the ultimate load-bearing capacity of soil over the in-situ condition.
What is Plate Load Test?
The Plate Load Test is an in-situ test carried out to obtain the ultimate bearing capacity of the soil, settlement of the foundation & allowable bearing pressure of the soil. A plate load test is appropriate for cohesionless soil where settlement takes place in a shorter duration. The importance of this test lies in the helpful factors in determining the best type of structural foundation.
Plate load test is performed under two methods:
1) Gravity load test (Reaction Loading method)
2) Reaction truss method
The plate bearing test is a field test used for in-situ site investigation that identifies a material’s CBR value as well as the ground’s ultimate bearing capacity and expected settlement under a certain load. This is undertaken in accordance with BS 1377 Part 9: 1990.
In this method statement, the focus is given to Gravity Load Test.
Plate Load Test Method Statement
1. Introduction
Description of the Project here: (xxxxxxx)
2. Site Location
Site location here: (xxxxxxx)
Refer to Location Map below:
(Location map here)
3. Purpose
This method statement presents the methodology to be implemented for the execution of the field Plate Load Test for (Name of Project here).
The purpose of this test is to evaluate the ultimate bearing capacity and deformation parameters of the soil beneath the plate without entailing the effects of sample disturbance.
4. Scope of Method Statement
This Plate Load Test Method Statement includes the determination of the vertical deformation and strength characteristics of soil in the field by assessing the force and amount of penetration with time when a rigid plate is made to penetrate the soil. The method may be carried out at the ground surface, in pits and trenches, or in adits.
5. Mandatory Requirements:
Induction and Training:
Safety and Health induction shall be conducted by the (Contractor name) Health & Safety Department prior to the commencement of works to each person involved in works. All technicians involved in the execution of the works and the workers who have undertaken critical tasks shall be competent and certified to undertake the works. All workers will receive a daily briefing about the work they are to undertake that day.
Instruction and Supervision
The Site Engineer is responsible for the job and proper execution of works in accordance with manufacturers’ instructions and approved method statements. He will be present at the site during working hours together with Safety Officers to monitor all activities and ensure the safety of the workers.
The Site Engineer will be in-charge and directly supervising Supervisors and Foremen, and carry the job at the site. Any completed activity must be channeled and coordinated with the Quality Department. Acceptance of completed activity in line with the approved ITP will be closed through Work Inspection Request (WIR) approval by the Supervision Engineer.
6. Preliminaries
Permits and Licenses
The Stakeholder and Permit Coordinator will be responsible acquire the Authority approval of the necessary permits required to commence site activities.
The following Permits are required and will be obtained:
Permit Scope Issued By
Permit To Work (PTW)
Utilities Clearance (Previous clearance applicable) xxxxxxx
Road Opening Clearance xxxxxxx
An approved Third Party Laboratory with Prequalification document per Appendix E will be tasked to carry out the plate load testing. Calibrated tools and equipment shall be used as per Appendix F.
7. Notice to Start (NTS)
The contractor will secure approval from the Supervision Engineer prior to starting any activity through the Notice to Start (NTS) submittal. The contractor will ensure that all relevant documents approval is in place as it is the primary requirement of NTS.
Notice to Start or NTS must be submitted 7 days from the start of the activity in order for Supervision Engineer to review and correlate the received relevant submittals with respect to the subsequent activity.
8. Work Execution
8.1 Bearing Capacity Parameters
(As per the project’s given value).
Testing Procedure
8.2 Reaction Loading System
The provision of the reaction load may be made in several different ways including Loaded truck/low bed/ excavator equipment which has a capacity of more than 10 tons.
Care shall be taken to ensure that the reaction load remains stable throughout the test without the possibility of the load tilting or collapsing.
8.3 Preparation at the Test Level
Carefully trim off and remove all loose material and any embedded fragments so that the area for the plate is generally level and as undisturbed as possible. Dune sand can be used to make the surface level if required.
Protect the test area and the plate load test apparatus from moisture changes, sunlight, and the effects of adverse weather as soon as the test level is exposed and throughout the test.
8.4 Preparation and Erection of Loading and Measuring Apparatus
Place in a convenient position the reaction loading, force measurement, and deformation measurement system ready for immediate erection as soon as the plate is in position.
Position the load centrally over the plate and make it vertical so that the reaction load is applied directly to the plate without eccentricity.
8.5 Incremental Loading Test
This test is suitable when the drained loading characteristics of the soil are required. In order to decide the loading for the increments make an initial estimate of the likely maximum load to be applied (Maximum load 100kN applied using 305mm diameter plate to verify 450kN/m2 (example-Based on Preliminary Report DS/642) (or use your project required bearing load) bearing pressure considering the factor of safety 3.)
Select at least five more or less equally spaced increments and apply the increments cumulatively to the plate.
Record the load for each increment and ensure that the load is kept constant.
Record the settlement under each load increment against time, commencing with the application of the load. Make frequent measurements in the early stages and increase the time interval between measurements as the settlement rate decreases.
Record the load for each decrement and ensure that the load is kept constant.
Record the settlement under each load decrement against time.
Note. The load should preferably be maintained at each increment until the penetration of the plate has ceased. This time will depend upon the soil type and the permeability.
8.6 Frequency of Testing
Following the Structural Notes under IFC Drawing at least two (2) plate load tests will be conducted and witnessed by the Supervision Engineer.
9. Quality
The Inspection and Test Plan (ITP) for Plate Load Test Method Statement summarizes various characteristics to be checked. The concerned Site Engineer or Site Supervisor will be responsible to ensure compliance for these operations and the site QA / QC Engineer will carry out quality control checks and report the inspection results.
9.1 Quality Records
a) Quality records shall be provided as identified in the ITP and maintained as per ISO 9001.
b) Standard form of records, quality checklists, and QA/QC reports requirements are defined in the Inspection and Test Plans.
9.2 Specific Quality Measurements
a. All works will be undertaken in compliance with the quality requirements of the Contract, and “Project Quality Management Plan”. Where non-conformance is found/identified to demonstrate its conformity. All works requiring inspection and testing to demonstrate conformity with requirements will be undertaken in accordance with the “Control of Inspection and Testing”.
b. Where non-conformities are found/identified, they will be addressed in accordance with “Procedure for Control of Non-Conformances”. The quality control activities associated with the works will be conveyed to all personnel involved in the execution of the works by the Project QA/QC Manager prior to the commencement of the work. The equipment and instruments used for measurements on-site will be calibrated and certified.
The relevant documents will accompany the corresponding equipment and instruments. Necessary internal and external training is provided to the staff carrying out the job to ensure that the quality standards required on the project are met. Skilled and competent personnel are deployed to undertake the job.
10. Health and Safety
10.1 Specific Health & Safety Requirements & Precaution Measures
The works shall be carried out in compliance with the applicable HSE legal and contractual requirements as well as Health and Safety Plan.
Any emergency situations that may occur on-site shall be dealt with following the procedures, responses, and controls as described in the Emergency Preparedness and Response Plan.
The significant HSE hazards and risks related to the works covered by this document have been identified, and documented in “Risk Assessment”.
The environmental hazards and risks shall be identified and documented in accordance with the Environmental Risk Assessment Plan.
The identified hazards and associated risks and mitigation controls shall be communicated to the workforce through registered Pre-task briefings at the beginning of each shift.
Daily task briefing shall be performed prior to the commencement of work.
This might interest you: Method Statement for Civil Engineering
10.1.1 Personal Protective Equipment
The minimum PPE as per the project HSE Plan that all personnel involved in the works will wear are:
• Safety Helmet
• Safety Shoes
• High Visibility Vest
• Protective eyewear (glasses)
• Gloves
• Ear Plug
Personnel not directly involved in physical work, who are visiting the site must also wear all the required personal protective equipment at any time they are outside of their vehicle, with the exception of gloves, which are discretionary. Personnel who are visiting the site but not leaving the PPE “free” designated areas which, if present on the site, will be clearly defined by signs and barriers (typically around the offices and car park), are not required to wear PPE (but it is recommended, especially protective eyewear).
10.1.2 Manpower
All personnel shall wear the required Personal Protective Equipment (PPE) in accordance with the Health and Safety Plan.
Any incident, injury, or near-miss will be reported immediately to the Safety Department and Site Manager.
The welfare facilities (see Health and Safety Plan) for the site work including a drinking water cooler, shaded area, worker’s toilet blocks, dedicated smoking area, and emergency standby vehicle will be established prior to commencing the works.
10.1.3 Plant and Equipment
All plant and equipment shall be inspected by the Plant & Equipment department prior to starting the work.
Before the use of any tool, inspection, and color coding is mandatory to ensure the smooth execution of work.
The subcontractor will also practice a daily visual inspection of all plants and equipment. A pre-shift visual inspection must be contacted and recorded as per the equipment checklist.
The following will be ensured as a minimum:
All equipment shall have valid certificates and inspections.
Plant/ machine operators will have all-around 360 degrees of visibility at all times.
Regular maintenance of the plant will be carried out as per the manufacturer’s recommendation.
Plant movement and operation will be coordinated and managed to ensure safe and efficient operation. All persons on site will be briefed on the hazards of working adjacent to traffic or in the vicinity of moving plant/ equipment & instructed to maintain eye contact at all times with machine/vehicle operators.
No sleeping or resting will be allowed underneath stationary plant/ equipment or vehicles.
10.1.4 Access / Egress on Work Site
Only authorized personnel will be permitted to enter the worksite. Upon arrival at the site, the following checks will be made and any non-compliance will result in that person being prevented from entering the worksite:
Evidence of receiving site-specific safety induction (register of attendance/ helmet sticker)
All staff shall have their ID card with them at all times, as evidence of site induction and competencies.
Appropriate Personal Protective Equipment (PPE)
At the end of each working day, all access to the worksite will be secured. A night-time patrol will ensure that the work area is secure and that safety precautions are in place. The following will be ensured as a minimum:
Access/egress routes shall be clearly defined by designated walkways/ traffic routes/ loading-unloading areas, signage/barriers & lighting.
Access/egress routes will not be blocked as a result of the work.
Access/egress for trench excavation shall be provided as per site requirements and Safety department inspection approval.
Vehicle traffic routes will be maintained as two-way streets.
10.1.5 Emergency Preparedness
All accidents/incidents and near misses shall be reported immediately to site management.
In the event of a serious accident, the area will be segregated and a full investigation will be carried out with an initial report submitted to the Client within 24 hours.
The contractor’s personnel will meet the emergency services at the site entrance and escort them to the scene of the accident.
Emergency contact names and mobile numbers are displayed in the site office and rest areas.
Fire extinguishers will be placed at designated points around the site office and welfare areas.
Mobile plant and equipment will have fire extinguishers fixed in place.
Smoking will only be allowed in designated areas.
Trained first-aide will be available on-site and first-aid kits available in the site offices.
Engineer, Supervisor, and Foremen shall be supplied with a complete set of First Aid Kit to be kept inside their vehicle in order to give immediate treatment in case of an accident happen.
10.1.6 Working at Night
In the case of the night, work will be carried out, the following should be ensured:
a) Checking the inventory of safety equipment to make sure they are sufficiently available, appropriate, and in good working condition. Retro-reflective signage, barriers, cones, signage, reflective tapes, and lighting equipment will be provided for nighttime construction works.
b) Scheduling of construction materials delivery at specific time intervals.
c) Large machinery movement will be directly supervised.
10.1.7 Medical / First Aid Facilities
Prior to the commencement of work, the confirmation will be made that all appropriate and required first aid facilities and trained first aid personnel are available on the site and if necessary, shall be made available for the prompt attention of the injured person.
For minor injuries, the contractor’s vehicle assigned to the job site will be used for transporting injured persons to the first-aid station. If the person needs transportation to the hospital, an ambulance will be required.
10.1.8 Site Security
Watchmen will be kept full-time on-site for security purposes.
10.1.9 Emergency Contact Numbers
The emergency contact numbers list shall be kept up to date at all times and shall be displayed on-site at such locations so as to be readable by all personnel.
Emergency Numbers
For Ambulance/Fire/Civil Defense
Call For Ambulance
Project Emergency Number
11. Environmental
11.1 Control Measures
Environmental control measures will be taken to avoid any leaks, and wastes to Environment which can pollute the environment. Environmental aspects will be assessed to control them.
a) Noise Control:
In case of high noise workers will be given hearing, protection devices, and efforts will be done to reduce the noise by taking engineering control.
i. To adequately define the noise problem and set a good basis for the control strategy, the following factors should be considered:
• Type of noise
• Noise levels and temporal pattern
• Frequency distribution
• Noise sources (location, power)
• Noise propagation pathways, through the air or through the structure
• In addition, other factors have to be considered: for example, the number of exposed workers, type of work, etc. If one or two workers are exposed, expensive engineering measures may not be the most adequate solution and other control options should be considered; for example, a combination of personal protection and limitation of exposure.
ii. General source Noise Control can involve:
• Maintenance of equipment (replacement/adjustment of worn/loose parts, balancing, lubrication)
• Substitution of materials
• Substitution of equipment
• Substitution of parts of equipment
• Change of work methods
• Substitution processes
• Substitution of Mechanical Power Generation and transmission equipment
• Replacement of worn moving parts
• Minimising the number of the noisy machine running at any time
b) Dust Control:
• Regular dust suppression on exposed bare ground and other areas susceptible to dust generation is required.
• During high windy weather conditions, the work may be suspended temporarily to prevent contributing dusty conditions on-site.
• Mandatory use of dusk masks inside the working zone areas.
• Vehicles transporting materials should maintain a speed limit of less than 10km/hr.
c) Waste Management:
The environmental manager in coordination with the health and safety manager shall ensure that the toolbox talks include aspects of the environment particular to the work execution and waste management will be:
i. Waste Reduction:
• Reduce waste generation and disposal.
• Select materials with increased product life reducing the overall amount of material sent to dumpsites/landfill.
ii. Waste Reuse:
• Reuse waste resources without further manufacturing.
• Review policies on the disposal of obsolete equipment or products with a focus on identifying alternate uses or users.
iii. Waste Recycle:
• Turning waste resources into similar or different products.
• Increase staff awareness in order to maximize co-mingled recycling and avoid contamination of recycling bins.
iv. Disposal:
• Spill kit should be provided
• All static equipment should be provided with a drip tray
• Training should be provided to control leakage from equipment
• All hazardous waste should be kept separately in red colored skips for proper disposal by an approved hazardous waste management agency
• All waste will be segregated into different skips provided at the site.
• All waste will be collected from the site in a separate labeled bin from where it will be disposed-off as per legal compliance.
• All waste generated such as concrete debris, shutters, and other construction waste debris shall be collected by the sub-contractor/supplier or Disposal Company and should be recycled.
v. House Keeping:
• Good Housekeeping of the workplace will be maintained after periodically cleaning the area and every possible effort will be done to make the environment neat and clean
12. Interface:
12.1 Interfaces
The following Interface departments permit shall be obtained.
Party Description
Sewage line & Road works interface
IT Line interface
Electrical & waterline utility interface
13. Resource Planning:
13.1.1 Personnel/ Workers
Construction Manager
Site Engineer
QA/QC Inspector
Safety Officer
Technician
All of the above will individually be responsible for a safe and healthy operational environment consideration of all the workers in their team related to the execution of their duties and any other personnel.
13.1.2 Equipment and Plate Load Test Apparatus
Reaction Load – Loader/JCB/Truck (or other equipment more than 10 tons) | 1 | To give the required load |
Plate | 1 | To know the settlement from the force applied |
Dial Gauge | 3 | To measure the settlement readings |
Stop Watch | 1 | To know the time interval to take readings |
Reaction Load – Loader/JCB/Truck (or other equipment more than 10 ton) | 1 | Load Provision |
The above tools and equipment shall be checked for operational suitability before each shift of commencement of works including, but not limited, to safety and operational compliance. The same shall be executed for all small tools and miscellaneous items.
The foremen and engineers who are on-site shall ensure that all necessary equipment is available as well as fit and safe prior to the commencement of work.
All the above plant and equipment shall comply with the followings;
c) All plants and equipment used in the works shall have a valid certificate of operation provided by a recognized licensing authority.
d) Plant operators shall hold a valid operator’s license.
14. Appendices, References
14.1 Appendices
a) Appendix A – Plate Load Test Method Statement Risk Assessment
b) Appendix B – Reference Drawings
c) Appendix C – Inspection and Testing Plan
d) Appendix D – Checklist
e) Appendix E – Copy of Third-Party Laboratory Approval
f) Appendix F – Calibration Certificates
14.2 References
a) Project Specification
b) IFC Drawings
c) BS 1377-9:1990 (Amd No. 17229, 2007) Test 4.1 – Determination of the Vertical Deformation and Strength Characteristics of Soil by the Plate Loading Test.
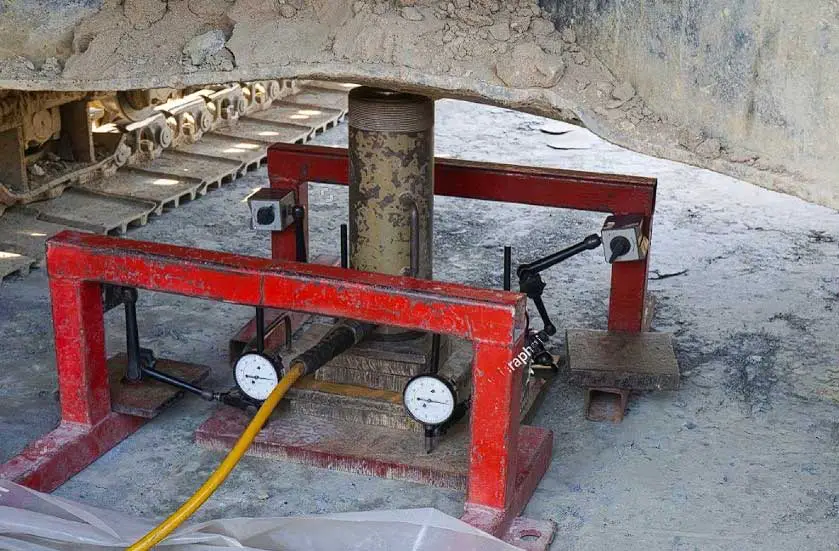