Table of Contents
Method Statement for Testing and Sampling Concrete
This method statement for testing and sampling concrete is applicable to taking concrete samples both before and during concrete pouring operations as well as performing the required tests.
This civil works method statement’s objectives are to establish and maintain efficient quality control systems, carry out the work by accepted standards and best practices, and do so at all phases and activities of concrete sampling and testing.
Abbreviations
Method Statement – MS
Inspection and Test Plan – ITP
Inspection and Test Request – ITR
Project Manager – PM
Construction Manager – CM
Personal Protective Equipment – PPE
ITL Independent Testing Lab – ITL
Applicable References and Standards
- BS 1881 Part 5, Methods of Testing Hardened Concrete for Other Than Strength
- BS EN 12350-1: 2000, Methods of Sampling Fresh Concrete
- BS EN 12350-2: 2000, Methods of Testing Fresh Concrete. Method for Determining the Density of Compacted Fresh Air Methods of Making & Curing Test Specimens Analysis of Hardened Concrete,
- BS EN 12350-6: 2000 Part 108 to Part 113 Part 124 Concrete Testing Methods
- BS EN 196 ASTM C 94/BS 5328 Ready-Mixed Concrete
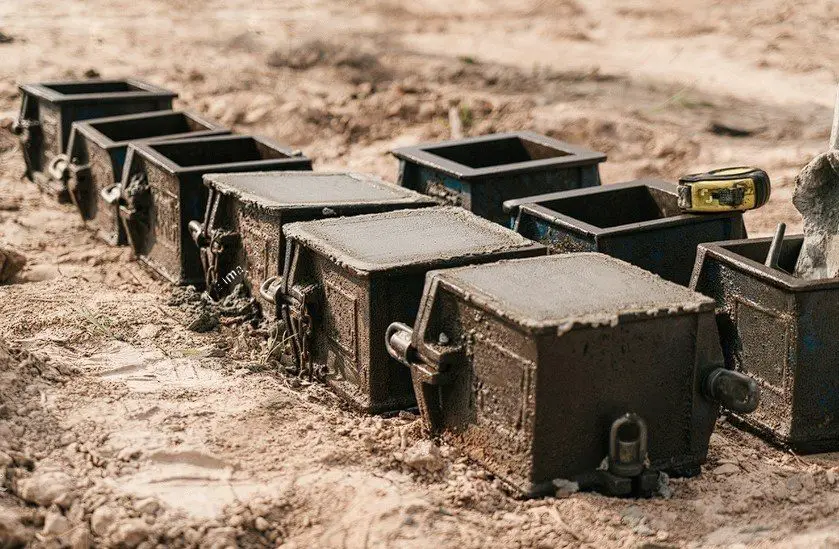
Equipment Required
Concrete Mixers
Slump Measurement
Cone and Equipment
Concrete Cube Moulds for Concrete Sampling Testing
Thermometer
Meter Tape
Curing Pool
Cube Crushing and Testing Equipment
Equipment for Durability Sampling and Moisture Content
Safety Equipment As Applicable
Concrete Sampling Procedure
Pre-sampling Activities:
All materials suggested for use in making concrete must be fully described. The consultant must first have approved the materials that make up concrete before it can be installed in the permanent works. Without the consultant’s approval, approved materials cannot be changed or replaced in the future.
All testing and sampling equipment must be calibrated. Every testing and sampling procedure must be carried out on location, in ITL, or the presence of an ITL representative.
Steps in Sampling
Every class of concrete in production at each facility must have a sample obtained for use in a project.
As instructed by the consultant, samples of concrete must be obtained at the mixing or depositing point.
By the sampling guidelines outlined in BS EN 12350-1:2000 (Testing new concrete), all samples must be taken in the presence of a representative from the contractor, consultant, or client, as applicable.
By the agreed-upon concrete grade and placement, samples must be taken on a basis of one for every 20 cubic meters of concrete poured or more frequently as necessary.
In any case, whichever frequency is greater, not less than one sample must be taken each day or for each pour of concrete that is laid. 6 x 150mm cubes from each sample must be cast, cured, and tested by BS EN 12390-1:2000.
Before casting cubes or measuring slump, any aggregate with a nominal size of 75mm that is retained on a 50mm sieve must be removed from the concrete.
As specified in BS EN 12390-1:2000 [Testing Hardened Concrete, Shape, Dimensions and Other Requirements for Specimens and Molds], six 200mm test cubes must be cast from each sample and cured.
In this situation, samples must be taken on a basis of one for every 100 cubic meters of concrete laid, but in any case, there must be at least one sample taken each day or for each pour of concrete, whichever is more often.
Concrete Testing
For all concrete production classes, three cubes must be tested at 7 days and three at 28 days, or as required by the client or consultant.
The results of the test will be referred to as one test based on the average strength of the three crushed cubes at & or 28 days.
Concrete will be considered to have the required strength if:
Any test result for that class of concrete must be at least 85% of the final trial mix strength.
The final trial mix strength for any class of concrete is not less than 90% of the average of any six consecutive test results for that class.
For that class of concrete, no single cube result falls below 75% of the final trial mix strength.
All tests must be performed by a testing organization that has been approved and has experience testing concrete.
Slump Test
For each batch from which samples are obtained as well as additional batches at the frequency agreed upon by all parties, the slump or compacting factor of the concrete must be determined.
At the time of sampling, the slump of each sample must be carried out by BS EN 12350-2: 2000.
Concrete can only be used for placement if, at the time of placement, its workability falls within one of the following limits:
The slump of the concrete in any batch must not deviate by more than 25 mm or one-third of the value established by trial mixes, whichever is larger.
If a compacting factor is used instead of a slump value, its value cannot vary more than these limits:
- For values of 0.9 or above ± 0.03
- For values between 0.8 and 0.9 ± 0.04
- For values of 0.8 or less ± 0.05
Water/Cement Ratio
The water/cement ratio as assessed from the slump test section findings above, or where required by the client, determined by samples from any batch, should not deviate by more than 5% from the stipulated maximum value or the value established during the trial mixes, whichever is the lower.
Testing for Air Content
Any specific batch of concrete must have an air content that is within +1.5 percent of the required value, as determined by individual samples obtained at the point of placement and representative of the batch.
The average percentage air content across any four determinations made in quick succession from different batches must fall within +1.0% of the required value.
For each batch, the air content needs to be verified.
Entrapped air that is still present after compaction is included in the total amount of air content.
Concrete Temperature Monitoring
Fresh concrete’s temperature must be tested for each sample, and the frequency of the measurements will depend on the demands of the contractor and the client.
Durability Tests
Concrete samples must coincide with samples collected from cube strength tests as necessary to be tested for durability attributes using the aforementioned absorption and permeability tests.
Chloride Permeability
According to AASHTO T277, chloride permeability. The most you may be charged after 28 days is 3500 for regular concrete or 1500 for GGBS concrete. The appropriate standard can be referred to for additional categories.
Maximum Water Penetration
According to DIN 1048, the maximum water penetration at 28 days for silica fume concrete and 15mm for regular concrete is 10mm and 15mm, respectively.
Initial Surface Absorption
In accordance with BS 1881-208:1996 [Testing Concrete. Recommendations for the Determination of the Initial Surface Absorption of Concrete [ISAT]. The maximum ISAT at 28 days (10-minute test) for both silica fume concrete and regular concrete must be 0.15ml/m2/sec.
30 Minute Absorption
BS 1881-122:1983 [Testing Concrete]. Method for Water Absorption Determination. For silica fume concrete, the maximum absorption must be 1.5% at 21 days, and for normal concrete, 2.0% at 21 days.
Test Frequency Rate for Concrete Tests
Requirement | Test Method | Test Frequency Rate |
Fresh Concrete | ||
Sampling | ASTM C 31/C 172 and C 192 | as required by a certain test |
Slump | ASTM C 143 BS 188 | 20 m3 for each production cycle |
Air Content | ASTM C 173 or C 231 | every 100 m3 during production |
Temperature | ASTM C 1064 | Every 20m3 during the production |
Hardened Concrete | ||
Sampling | ASTM C 823 and BS 1881 Part 101 | As required by individual test |
Strength (cubes) | BS 1881 Part 108 | Six cubes every 20 m3. 3 Cubes for 7 days and 3 Cubes for 28 days. |
Strength (drilled cores) | ASTM C 42 | As required if cube tests do not meet acceptance criteria. No. of cores as instructed by the engineer |
Cement Content | ASTM C 85/C 1084 | As required if cube tests do not meet acceptance criteria. No. of cores as instructed by the engineer |
Rapid chloride permeability test (RCPT) | ASTM C 1202 | As required if cube tests do not meet acceptance criteria. No. of cores as instructed by the engineer |
Water penetration | DIN 1048 | Three tests every month for the first three months of production then every three months |
Porosity | RILEM CPC 113 | Three tests every month for the first three months of production then every three months |
Water absorption | ASTM C 642 | Three tests every month for the first three months of production then every three months |
Total chlorides | ASTM C 1152/C 1218 BS 1881 Part 124 | Three tests every month for the first three months of production then every three months |
Total sulphates | ASTM C 856 BS 1881 Part 124 | Three tests every month for the first three months of production then every three months |
Testing Agencies
After the first three months of production, tests are conducted every three months.
One of the Independent Test Laboratories (ITLs) or Approved Testing Agencies (ATAs) shall perform the testing services. Testing Services must be paid for by the Contractor.
Procedure for Quality Control During Concrete Sampling
Before incorporating any materials into the job and after they have been approved by the consultant, the QA/QC Engineer is in charge of verifying them all.
The Check Sheets’ elements will be verified by the QA/QC Engineer/Inspector, who will also physically check that the area is prepared for testing and sampling.
After verifying all elements, the QA/QC Engineer will provide the consultant for inspection or witness the ITR or other pertinent testing and sampling information.
A new inspection or testing will be conducted if any corrections are required, and the QC Engineer will notify the ITL/Site Engineer of the problem.
ITL will carry out the testing or sampling of concrete following client consent.
In accordance with the delivery note, the stipulated testing frequency, and the specification and method statement for concrete sampling and testing, the ITL will verify the ambient temperature, concrete temperature, slump, and mix details.
As per the specification and method statement for concrete sampling and testing, ITL will carry out the required sampling and testing for compression strength test at the stated testing frequency.
ITL will conduct 7-day compression strength tests, followed by a 28-day test (if the 7-day test fails, the client will be informed right away).
QA/QC Engineer will send ITR to witness/Test request to archive for the creation of close-out dossiers after getting client permission.
Attachments
Inspection and Test Plan
Checklist
Quality Control Procedures
Risk Assessment
tag: # Method Statement for Testing and Sampling Concrete