Table of Contents
- What is the Method Statement for Street Lighting Installation?
- Overview
- Abbreviations
- Safety and Health Measures
- Methodology
- Storage and Care of Materials
- Fitting and Installation
- Responsibilities
- Waste Disposal
- Safety and Environment Control
- Quality Assurance and Quality Control Measures
- Testing and Commissioning
What is the Method Statement for Street Lighting Installation?
The Method Statement for Street Lighting Installation is a comprehensive document that outlines the standardized procedure for provisioning and installing street lighting infrastructure.
This MS document covers essential aspects such as preparation, material delivery and inspection, system installation, and adherence to safety standards, ensuring that all processes are executed per the project’s quality and safety requirements, from start to finish. It serves as a guide for project managers, installation crews, and quality control personnel to maintain consistency, efficiency, and compliance throughout the installation process.
Overview
The intent of this document is to outline the procedure for the provisioning and setting up of Street Lighting. It encompasses the following aspects:
Preparatory steps for the operation.
Receipt and examination of materials upon delivery to the construction site.
Execution of the street lighting system installation.
Abbreviations
PSP: Project Safety Plan
HSE: Health, Safety, and Environment
MS: Method Statement
ITP: Inspection Test Plan
INR: Inspection Request
MIR: Material Verification Record
QA/QC: Quality Assurance / Quality Control Engineer
Safety and Health Measures
Compliance with the material manufacturer’s Health and Safety guidelines is mandatory.
All workers are to be informed about these guidelines.
Relevant safety protocols must be adhered to, as detailed in the project safety plan.
Methodology
Materials
- Street Lighting Poles: Various types such as steel, aluminum, or concrete; selected based on height, design, and environmental considerations.
- Luminaires / Light Fixtures: LED, High-Pressure Sodium (HPS), Metal Halide (MH), etc.
- Bulbs / Lamps: Corresponding to the fixture type; LEDs are increasingly common for energy efficiency.
- Mounting Brackets and Hardware: For attaching fixtures to poles or other surfaces.
- Wiring and Electrical Cables: Insulated conductors suitable for outdoor use, of appropriate gauge as per the lighting system’s requirements.
- Conduits or Ducts: Metallic or plastic tubes to protect electrical wiring, complying with electrical codes.
- Grounding Equipment: Ground rods, clamps, and wires to ensure proper earthing of electrical systems.
- Connectors and Junction Boxes: For making electrical connections and housing wires.
- Foundation Materials: Concrete, rebar, anchor bolts for setting light poles.
- Isolators / Circuit Breakers: To safely manage electrical flow to the lighting units.
- Control Gear / Ballasts (if required): For certain types of lights such as HID.
- Photocell or Timer Systems: To control lighting based on daylight or time settings.
- Surge Protection Devices: To protect systems from electrical surges.
- Lighting Control System Components (if applicable): For smart lighting or remote-control functionalities.
The materials employed shall be pre-approved by the supervising engineer.
The sizing, as well as the placement instructions, will follow the approved shop drawings.
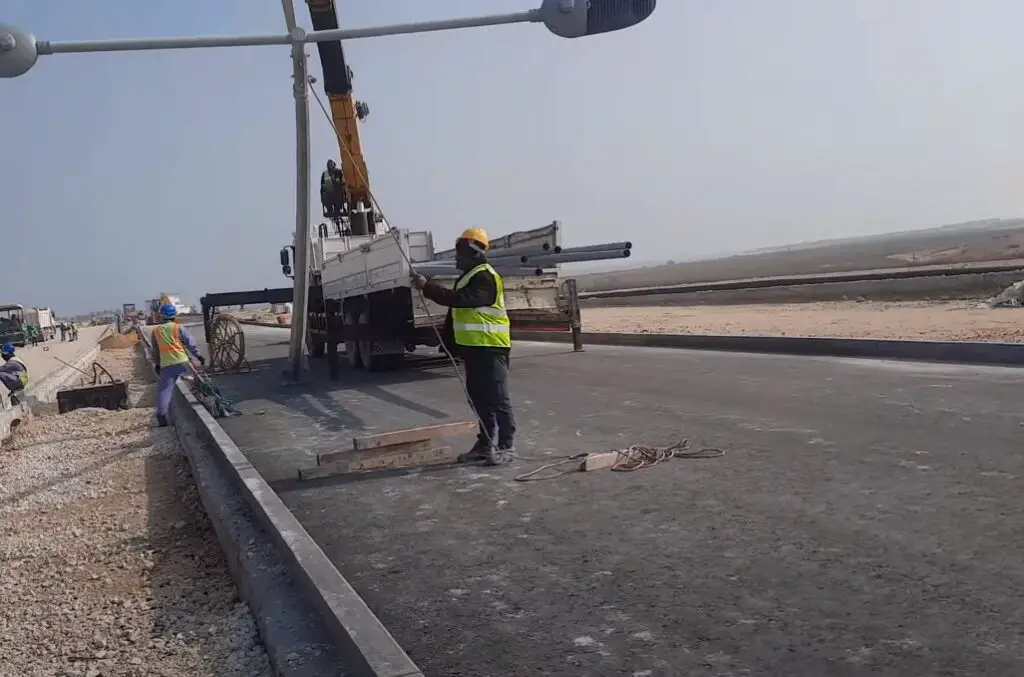
Equipment
Crane or Lifting Equipment: For hoisting light poles and luminaires into place.
Drilling Equipment: Such as augers or earth drills for pole foundation holes.
Concrete Mixer and Tools: For preparing and pouring pole foundations.
Hand Tools:
- Screwdrivers (Various sizes)
- Spanners and Wrenches
- Wire Strippers/Cutters
- Pliers (Needle-nose pliers, Side-Cutting Pliers, etc.)
- Hacksaw
- Hammer
- Allen Keys
- Level (Spirit or Laser)
- Tap measure
Electrical Tools:
- Electrical Drill and Drill Bits
- Voltage Tester / Multimeter
- Insulation Resistance Tester
Working at Height Equipment:
- Ladders or Scaffolds
- Safety Harnesses and Lanyards
Personal Protective Equipment (PPE):
- Hard Hats
- Safety Glasses
- High-Visibility Vests
- Protective Gloves
- Safety Boots
- Ear Protection (if necessary)
Traffic Safety Equipment: Cones, barriers, signs, and warning lights for roadside works.
Material Handling Equipment: Pallet jacks, dollies, or forklifts if required to move materials.
Temporary Lighting: For night-time or low-visibility working conditions.
Vehicle or Trailer: For transporting poles, luminaires, and large equipment to the job site.
Shoveling and Digging Tools: Spades, post hole diggers for manual excavation work.
Storage and Care of Materials
Transportation of parts to site should be identifiable in line with shop and certified CAD drawings.
Materials are to be stored as specified by the manufacturer, ensuring they are shielded from weather and onsite activities.
Fitting and Installation
Preliminary Steps:
Prior to installation, there will be a verification of materials and associated documents to ensure they meet the approved types.
Before initiating the installation, it’s critical to make sure that the designated areas are prepared, accessible, and in a proper state.
All related electrical work should be completed, tested, and approved by the Consultant.
Survey the installation locations to verify readiness.
Check that hand holes and cable underground ducts are ready.
Confirm readiness of concrete bases to match the specificities of each lighting unit.
Installing Street Lighting Columns:
By using a crane, hoist the street light columns and place them on their concrete foundations, aligning the embedded bolts with the base holes of the columns.
Confirm the columns are firmly situated and properly aligned, in compliance with the manufacturer’s guidelines.
Wire power cables to the internal isolator/circuit breaker and confirm secure connections. Ground the lighting column.
Mount lamp enclosures onto the columns. Verify lamp types and colors against approved specifications.
Attach light fixture diffusers and reflectors, ensuring alignment and secure attachment.
Connect a temporary power supply to test the operation of the lights.
Submit an Inspection Request for the light installation.
Setting up Flood Lights:
Install brackets for mounting flood lights, ensuring they are secured firmly.
Mount the flood lights onto the brackets and connect power cables to the fittings. Ground the lights’ bodies.
Install approved lamps onto the fixtures.
Apply a temporary power connection to test flood lights’ functionality.
Submit an Inspection Request for the installed flood lights.
Fitting Indirect Lights:
Secure the brackets for indirect lights at their specified locations, guaranteeing a rigid fixation.
Mount indirect light fixtures onto the brackets.
Link power cables to the light fixtures and certify proper connections and grounding.
Install lamps, verifying type and color correctness against approved specifications.
Check the operation of indirect lights with a temporary power supply.
Submit an Inspection Request for the indirect lighting installation.
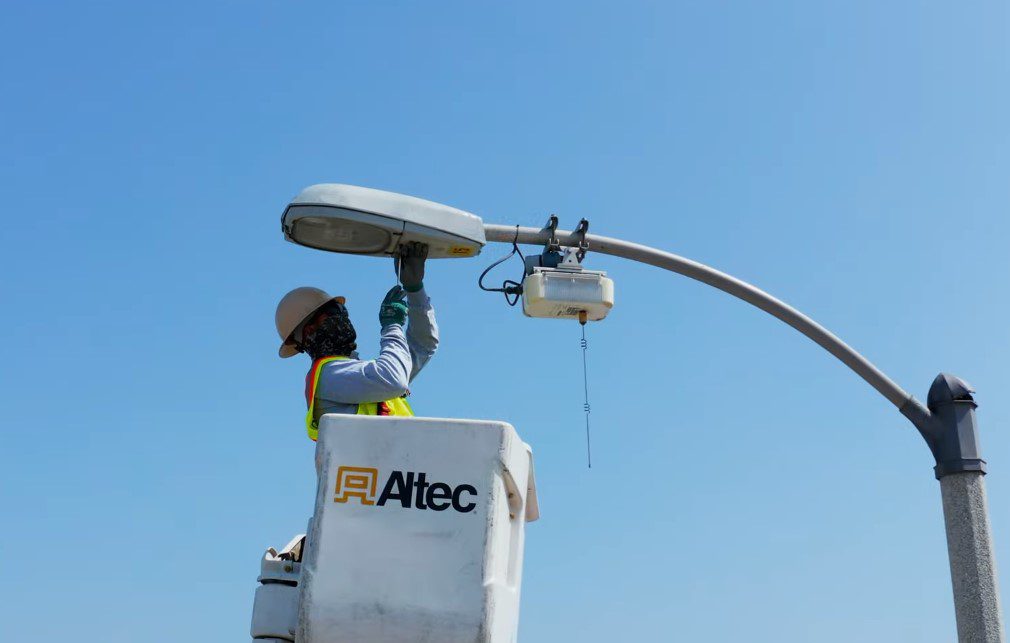
Technical Guidance:
Post-installation, the system technician will train the client’s designated technician for the system operations.
Training sessions are to be scheduled as per staff availability and duly recorded.
An INR for consultant’s approval will be issued after ascertaining that the system’s installation complies with approved drawings, specifications, and manufacturer’s recommendations.
Responsibilities
Project Manager:
Guarantee the preparation and application work adheres to Contract Specifications and approved drawings.
Ensure that work progression aligns with the planned schedule and approved method statement.
Make sure all necessary materials and equipment are available in accordance with the construction schedule.
Liaise with the main contractor, MEP coordinator, and Safety Officer for safe and proper work execution.
Site Engineer:
Ensure contract specifications, method statements, and shop drawings guide the work.
Distribute relevant information and responsibilities within the construction team.
Monitor work progress compared to the program schedule and report to the Project Manager.
Work in conjunction with the safety officer to maintain safe work practices.
Foreman:
Maintain daily coordination with the site engineer to efficiently distribute the workforce.
Confirm that assistant foremen are well-informed about their duties.
Coordinate manpower movement and resource requirements with the site engineer.
Ensure work area cleanliness and compliance with safety measures through coordination with the safety officer.
Notify the site engineer about areas ready for inspection.
Foreman along with the storekeeper are responsible for material distribution and control.
Safety Engineer:
Implement all safety measures following the HSE plan and ensure widespread awareness for its execution.
Confirm adequacy of applied safety measures to maintain a safe work environment.
Provide training to personnel to prevent accidents and maintain high safety standards.
Keep the work site orderly and clear of hazards.
Technician from the Supplier:
Execute work and allocate resources in collaboration with the sub-contractor’s Site Engineer daily.
Document daily progress and coordinate for upcoming plans with the Site Engineer.
Adhere to safety and engineering standards as set by the sub-contractor.
Promptly address unexpected issues or needs and relay information to the Site Engineer.
Storekeeper:
Oversee storage operations to ensure safekeeping of materials from rust and damage.
In coordination with QA/QC and respective engineers, acknowledge receipt of materials at the site.
Labor Requirements
Supervisory personnel and skilled technicians.
Tools Required
The following tools will be utilized for the installation of lighting fixtures:
- Screwdrivers
- Hacksaw
- Needle-nose pliers
- Electric drill and bits (for surface-mounted installations)
- Cutting pliers
- Wire strippers/cutters with spring
- Side-cutting pliers
- Leveling tool
- Shank screwdriver
- Electrical tape
- Voltage tester
Personal Protective Equipment, including safety helmets, boots, gloves, and vests.
Waste Disposal
Generated waste from the scope of works will be responsibly transported to the designated dump sites.
Safety and Environment Control
General control measures for safety, environment, and quality will be in effect:
- Suitable PPE must be worn at all times.
- Work permits must be secured for elevated work (> 2m), lifting operations (crane use), and confined space entry.
- Method statements and risk assessments approved in advance will be accessible on-site.
- All work participants must be briefed on method statements and risk assessments.
Specific safety measures that need to be followed during the street lighting installation process:
- Personal Protective Equipment (PPE): All personnel must wear appropriate PPE, including but not limited to helmets, safety glasses, gloves, high-visibility clothing, and safety boots.
- Electrical Safety: Ensure all electrical work complies with local regulations and standards; use electrical tools that are properly insulated and ground all electrical systems.
- Work at Height: Utilize proper fall protection systems when installing poles and fixtures at height. This can include harnesses, lanyards, guardrails, and lifelines.
- Traffic Control: Implement traffic management plans to protect both workers and the public when installations occur near or on public roads.
- Lifting Operations: Follow regulated procedures for crane or lifting equipment operation. Use appropriate lifting gear and ensure that operators are trained and certified.
- Tool Safety: Ensure that all tools and equipment are in good working order, regularly inspected, and used properly.
- Site Access: Restrict access to the installation site to authorized personnel only.
- Training: Ensure that all personnel are adequately trained in the tasks they are performing, particularly with regard to handling specialized equipment or materials.
- Emergency Procedures: Have clear and practiced emergency response procedures in place, including ready access to first aid and accident reporting.
- Environmental Precautions: Take measures to minimize environmental impact, such as avoiding contamination through oil leaks from machinery, or ensuring that no waste or debris is left behind.
- Manufacturer’s Instructions: Always follow the manufacturer’s instructions for the installation of specific components and systems.
- Housekeeping: Keep the site clean and free from trip and fall hazards. Properly store tools and materials when not in use.
- Pre-task Planning: Conduct daily briefings to discuss the tasks at hand, potential hazards, and the safety measures required for the day’s work.
- Work Permits: Secure the necessary work permits, especially for tasks that involve high-risk activities or areas with restricted access.
Each project will have its own specific set of safety measures detailed in the project safety plan, which must be tailored to the unique risks and conditions of the project site. The safety plan should also comply with all local legislation and industry best practices.
Quality Assurance and Quality Control Measures
The quality control (QC) and quality assurance (QA) aspects of a Method Statement for street lighting installation are critical components to ensure the structure is built to specifications and will perform as designed.
Quality Assurance (QA):
Pre-Installation Training: Providing training for installation teams on standard procedures, safety protocols, and specific equipment to be used.
Project Documentation: Maintaining thorough documentation throughout the project lifecycle, including design records, material purchase orders, and inspection reports.
Quality Control (QC):
Incoming Material Inspections: Regularly inspect materials upon delivery to the site for damage, defects, and conformance with specifications.
Installation Inspections: Regular checks during installation to ensure workmanship quality and adherence to the design plans and standards.
Testing and Commissioning: Conducting a series of tests to ensure the lighting system functions correctly. This might include photometric testing, electrical tests (insulation resistance, continuity), and functional testing of control systems.
Audits and Reporting: Periodic audits performed by QA/QC engineers to ensure that the project complies with the stated quality plan and all regulatory requirements.
Compliance Review: Verification against local codes, national standards (such as ANSI, IEC, etc.), and any client or project-specific requirements.
Corrective Action: Implementing corrective action procedures when defects or deviations from the intended quality standards are found.
Final Acceptance Inspections: Before project handover, performing final inspections to ensure that all quality criteria have been met.
Common Across QA and QC:
Inspection Test Plans (ITP): Creating and following an ITP that outlines the testing protocols and acceptance criteria for different stages of the installation.
Quality Control Checks:
- Visual inspections of trenching, conduits, and pole placement.
- Torque testing on bolts and fasteners.
- Ground resistance testing for electrical safety.
Quality Records: Keeping detailed records of all QA/QC activities, including checklists, inspection reports, test results, non-conformance reports, and corrective actions.
Communication and Coordination: Regular meetings and communication between the project management team, site supervisors, QA/QC personnel, and contractors to align on quality standards and address any concerns.
Testing and Commissioning
During the testing and commissioning phase of street lighting installation, several specific tests are conducted to ensure that the lighting system is safe, functional, and meets all necessary standards and specifications. Here are some of the key tests performed:
- Visual Inspection: Prior to activating the power, a thorough visual inspection is conducted to confirm proper installation of poles, fixtures, wiring, and other components. This ensures that there are no obvious defects or installation errors.
- Continuity Testing: Ensures that the electrical circuits have been installed correctly without any breaks that could affect functionality and includes verifying the continuity of conductors, grounding systems, and electrical connections.
- Insulation Resistance Testing: Performed to ensure that the insulation of electrical cables and components is intact, preventing potential short circuits or electrical hazards due to damaged insulation.
- Earth Resistance Testing: Measures the efficiency of the grounding system to ensure the electrical system can safely dissipate currents into the ground, thus protecting against electrical shock and equipment damage.
- Polarity Testing: Confirms that the electrical connections are connected in the correct polarity, which is vital for the proper operation of the lighting system and safety.
- High-Potential (Hi-Pot) Testing: Applies higher voltage than normal operation to cables and equipment to ascertain the adequacy of electrical insulation and to detect any material or workmanship defects that could cause operational issues.
- Functional Testing: Includes powering up of the lighting fixtures to verify operational functionality, such as lighting up at the correct brightness and responding appropriately to control inputs like photocells or motion sensors.
- Photometric Testing: Measures the light output, distribution, and uniformity to ensure it complies with the project’s lighting design requirements. This can include verifying lux levels (light intensity) at the roadway or ground level.
- Luminaire Tilt and Orientation Check: Ensures all lights are correctly aimed and oriented to provide the desired spread of light and minimize glare or light pollution.
- System Integration Test: If a lighting control system is in place, this test verifies that it is properly integrated with the lighting fixtures and responds as expected to command and scheduling.
- Torque Testing: Analyzing the tightened bolts and other fastening devices to confirm they’re adequately torqued as per specifications to maintain stability and safety.
- Load Tests: Verifying that the system is capable of handling the anticipated electrical load without overheating or showing signs of stress.
- Timer/Photocell Test: For automated lighting systems, tests are done to verify that lights turn on and off at the predetermined times or lighting levels.
- Thermal Imaging: To detect any hot spots in the electrical system that could indicate overloading, poor connections, or potential failure points.
Completion of these tests successfully confirms that the street lighting installation has been performed correctly, is safe for operation, and meets all the required performance criteria. Any issues identified during this phase need to be addressed and rectified before the system can be fully commissioned and handed over for public use.
tag: # Method Statement for Street Lighting Installation