Table of Contents
What is the Method Statement for General Pumps?
A Method Statement for General Pumps outlines the procedures and safety measures to be followed when installing, operating, and maintaining general pumps. The specific content of the method statement can vary depending on the type of pump, the application, and any relevant industry or regulatory standards.
Scope of Work
This project’s scope encompasses the installation and rigorous testing of various pump types within the company’s system. Additionally, it defines the corresponding duties and obligations.
Referenced Standards
- ISO 9001-2015
- ASME B16 – Specifications for Pipe Flanges And Flanged Fittings
- UL 448 – Standards for Pumps Intended for Fire Protection Service
- NEMA-G for Motors 15 HP and above
- Manufacturer’s Standards for Motors 15 HP and below
- Project Specifications as outlined in Division 21, titled “Electric-Drive, Centrifugal Fire Pumps & Diesel-Drive, Centrifugal Fire Pumps,” encompassing fire pumps, pressure-maintenance pumps, and fire-pump controllers.
- Relevant additional codes and standards.
- AWWA C 151 & C111 – American Water Works Association standards
- NFPA-20 – National Fire Protection Association Standard
Responsibilities
The Engineering Department is tasked with the pump selection process in alignment with the specifications outlined in the project documentation. Upon selection, the department will compile the necessary technical information and submit it for approval. The subsequent procurement process will adhere to the guidelines specified in the project’s quality plan.
The Site Engineer holds responsibility for overseeing the successful execution of the installation and commissioning phases.
The Site Mechanical Engineer assumes a comprehensive role, overseeing the entire execution process and actively monitoring in accordance with approved manufacturer recommendations.
The Quality Control (QC) Inspector is responsible for conducting inspections associated with this specific activity, working in coordination with the client’s inspection team.
QC inspection of received materials falls within the purview of the QC Inspector, who is also responsible for validating documentation accuracy in accordance with the provided technical submittal.
Procedure
The inspection and verification process involves ensuring the physical integrity of essential components, including the pump skid, pump, driver, auxiliary piping, and other related elements, to confirm the absence of any physical damage.
Separately shipped loose components and materials are cross-referenced with provided packing lists to ensure accuracy, while corrosion-resistant metal tags are affixed for identification.
The vendor is required to furnish the purchaser with detailed instructions for maintaining equipment integrity during storage and preparation on-site prior to start-up.
In addition to being stamped on the nameplate, pump serial numbers are clearly and permanently marked on the pump casing. Rotation arrows are either cast into or affixed to major rotating equipment components at easily visible locations.
Verification is conducted to confirm alignment of the pump skid’s layout with the Pump Piping and Instrumentation Diagram (P&ID).
Castings undergo visual inspection to ensure structural soundness, absence of defects (such as porosity, cracks, and scale), and proper finishing in accordance with MSS-SP-55 standards. Mold-parting fins, gates, and risers are meticulously removed or treated as necessary.
Fabricated steel casings and nozzle heads adhere to ASME B 16.1 standards for flange specifications.
Gasket contact surfaces are examined to ensure they are free from mechanical or corrosion damage.
Vent and drain configurations adhere to the requirements stipulated in the International Fire Code (IFC) and align with AWWA C-512 standards.
Exposed shafts and shaft couplings are enveloped in waterproof, moldable waxed cloth or volatile corrosion inhibitor paper. Seams are securely sealed with oil-resistant adhesive tape.
Equipment rigging and lifting procedures strictly follow the manufacturer’s instruction manual.
All piping components are meticulously placed in their designated positions as indicated in the P&ID, encompassing piping, removable pipe spools, valves, vents, drains, spectacle plates, blinds, flange spacers, and related elements.
In-line equipment and instruments are strategically positioned in accordance with the P&ID, encompassing items such as strainers, straightening vanes, flow meters, orifice fittings, pressure indicators, temperature indicators, and more.
Discharge and suction piping are clearly marked with flow directional arrows, fluid service details, line designation numbers, sizes, classes, and specifications.
The positioning and interspacing of supports for both inlet and outlet piping are in accordance with the specified support details outlined within their respective International Fire Code (IFC) drawings.
The inlet and outlet pipe spools undergo rigorous testing procedures.
Pipe alignment mandates complete contact with the designated supports, with the provision of shims as necessary to achieve the desired alignment.
Pressure gauges installed align with the range specified in the Piping and Instrumentation Diagram (P&ID).
Control valves, check valves, and globe valves (where applicable) follow the process flow direction as indicated.
The final cold alignment of components adheres to the permissible tolerances set by the equipment manufacturer.
The safety officer conducted testing to verify the functionality of lifting equipment.
External coatings applied to the piping are comprehensive and in adherence with the coating requirements specified for the project.
Package base plates are designed with a drain-gutter configuration, featuring one or more drain connections for efficient drainage.
Lifting lugs are integrated into the base plates, enabling a secure four-point lift operation.
Installation and leveling of mounting plates for pumps entail drilling base plate pads for all pump types.
For any given equipment support foot, a maximum of five shims is permissible.
All base plates intended for permanent installation within onshore facilities must undergo grouting procedures.
The vendor is responsible for commercial sandblasting of grout contact surfaces on the base plate in compliance with SSPC SP 6 standards. These surfaces are then coated with inorganic zinc silicate to prepare for subsequent epoxy grouting.
Equipment base plate mounting surfaces undergo meticulous longitudinal and transverse leveling, ensuring deviations are within 400 micrometers per meter (0.005 inches per foot).
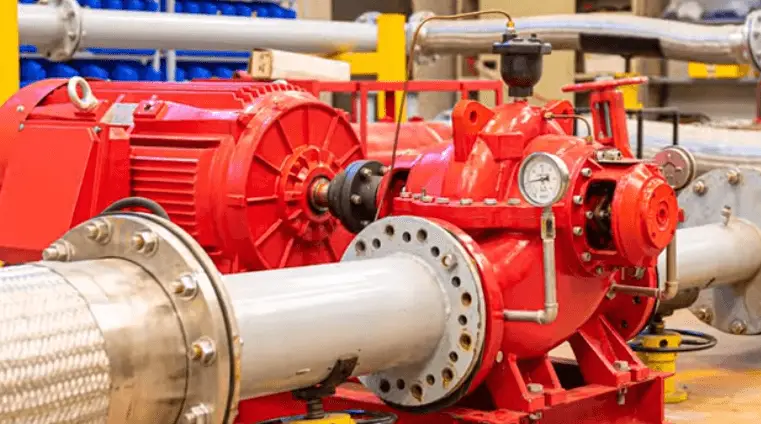
Final Pump and Driver Alignment
A meticulous evaluation of soft foot conditions is conducted, with the disconnection of piping from each equipment foot. It is crucial to acknowledge that the maximum acceptable displacement for each foot is 0.05 millimeters (2 mils), or as expressly specified by the equipment manufacturer.
Alignment procedures are meticulously executed within the confines of the manufacturer’s stipulated tolerances prior to the attachment of piping and conduit. Thorough pipe strain assessments are conducted following the manufacturer’s established protocols. Alignment is reconfirmed to adhere to the manufacturer’s tolerances after the integration of pipe and conduit.
The conclusive alignment procedure is carried out subsequent to the hydrostatic testing of piping and the successful completion and acceptance of piping support systems.
It’s noteworthy that, following the final tightening of piping bolts, an additional validation of shaft alignment is performed. Furthermore, all machinery undergoes manual rotation to verify the absence of binding or any detrimental case distortion that may have occurred during the piping installation process.
During the conclusive shaft alignment checks, the installation of piping spring hanger and spring support stops is carried out.
References:
- Checklists
- Inspection and Test Plan
Field Quality Control
Inspection and Testing Protocol Sustaining quality is achieved by methodically executing this protocol and guaranteeing the generation of essential quality documentation, as outlined in the attached formats accompanying this procedure and within the Inspection and Test Plan (ITP) for Pump Installation.
Cleaning and Site Preparation
Maintain a clean work environment by systematically clearing debris and dirt as work advances.
Materials Storage and Handling
On-site material storage is vigilantly overseen by qualified storekeepers to ensure optimal conditions and safeguard against environmental factors that may jeopardize their integrity (e.g., moisture, heat, dust, friction).
Materials shall be securely housed and organized within a controlled and secure area to mitigate deterioration and harm. Incoming materials are meticulously examined to ensure alignment with project specifications.
During handling, comprehensive care is imparted to all equipment and materials, a process overseen by both engineers and foremen to further reinforce the handling process’s reliability.
Health and Safety Measures
International Health and Safety standards are consistently applied on-site through the expertise of our proficient health and safety officers and engineers. This approach is designed to proactively avert hazards and uphold safety protocols that forestall potential serious injuries. Adherence to approved Personal Protective Equipment (PPE) is compulsory.
Environmental Considerations
All construction activities are executed to uphold supreme quality standards while concurrently avoiding any practices that may jeopardize the environment. Therefore, meticulous consideration is given to selecting environmentally friendly materials.
Any materials of hazardous nature are subject to careful storage, as previously mentioned, and proper disposal methods are adopted for scrap materials to ensure their safe handling.
Appendices
a. Risk Assessment Sheet